Zinc-nickel alloy electroplating process for metal surface
A technology for electroplating zinc-nickel and alloying processes, applied in the electrolysis process, electrolysis components, cells, etc., can solve the problems of cumbersome process, uneven thickness of electroplating layer, influence of mass transfer process, etc., to improve uniformity and speed, improve electroplating The effect, the effect of the simple electroplating process
- Summary
- Abstract
- Description
- Claims
- Application Information
AI Technical Summary
Problems solved by technology
Method used
Examples
Embodiment Construction
[0028] The present invention provides a technical solution: an electro-galvanized nickel alloy process for metal surfaces, comprising the following steps:
[0029] S1. Raw material inspection: inspect the metal components to be electroplated, including the completeness, material and hardness of the metal components;
[0030] S2, chemical degreasing: use lye to remove the saponified grease by saponification of the grease attached to the surface of the metal component;
[0031] S3, a water wash: use the flowing hot water to wash the metal components after degreasing in step S2;
[0032] S4, electrochemical degreasing: transfer the metal component after S3 washing to the electrode of the alkaline electrolyte, and use the polarization of the electrode during electrolysis to reduce the surface tension of the solution interface to achieve the secondary degreasing effect;
[0033] S5, secondary water washing: using the flowing hot water again to wash the metal components after the s...
PUM
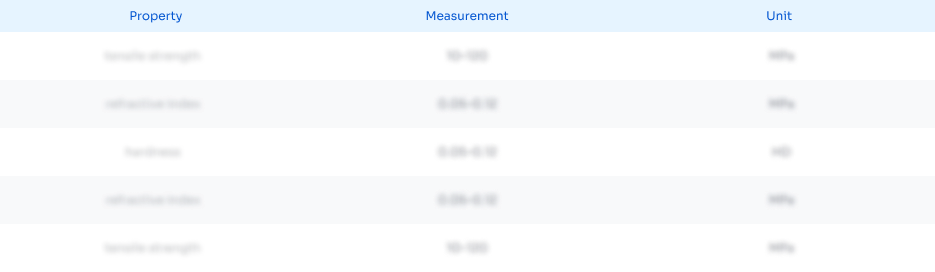
Abstract
Description
Claims
Application Information

- R&D
- Intellectual Property
- Life Sciences
- Materials
- Tech Scout
- Unparalleled Data Quality
- Higher Quality Content
- 60% Fewer Hallucinations
Browse by: Latest US Patents, China's latest patents, Technical Efficacy Thesaurus, Application Domain, Technology Topic, Popular Technical Reports.
© 2025 PatSnap. All rights reserved.Legal|Privacy policy|Modern Slavery Act Transparency Statement|Sitemap|About US| Contact US: help@patsnap.com