Production method of EH420-grade 150 to 200mm extra-thick steel plate
A technology of extra-thick steel plates and production methods, which is applied in the field of steel for marine engineering, can solve the problems of strict quality requirements for continuous casting slabs, limit the thickness of finished steel plates, and affect the low-temperature impact toughness of steel plates, etc., and achieve a significant effect of grain refinement, Effect of improving toughness and plasticity and improving welding performance
- Summary
- Abstract
- Description
- Claims
- Application Information
AI Technical Summary
Problems solved by technology
Method used
Image
Examples
Embodiment Construction
[0030] A production method of EH420 grade 150-200mm extra-thick steel plate, its chemical composition and mass percentage are as follows: C: 0.05%-0.09%, Si: 0.20%-0.50%, Mn: 1.40%-1.70%, P≤0.015% , S≤0.005%, Nb: 0.030%~0.080%, V: 0.001%~0.050%, Al: 0.01%~0.05%, Ti: 0.005%~0.020%, Mo: 0.00%~0.08%, Cr: 0.15% ~0.35%, Cu: 0.10%~0.50%, Ni: 0.01%~0.80%, Cr+Ni+Mo+Cu≤1.30%, the balance is Fe and unavoidable impurities;
[0031]The continuous casting slab with a thickness of 320mm is heated at 1160-1200°C, and rolled in one stage. Before the last rolling, it is cooled by laminar flow and reddened, and then rolled to the thickness of the finished product; it is cooled to 400-400°C through controlled acceleration. 500°C, when the accelerated cooling is controlled, the cooling red temperature is below 450°C, and finally air-cooled to room temperature. Among them, rolling is carried out in the recrystallization zone, and the reduction rate of each pass is > 10%; before the last rolling p...
PUM
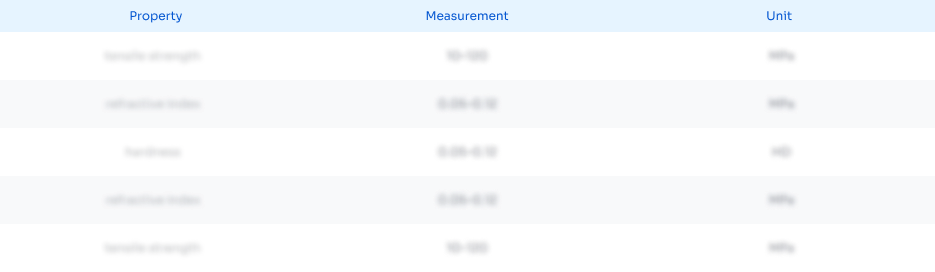
Abstract
Description
Claims
Application Information

- R&D
- Intellectual Property
- Life Sciences
- Materials
- Tech Scout
- Unparalleled Data Quality
- Higher Quality Content
- 60% Fewer Hallucinations
Browse by: Latest US Patents, China's latest patents, Technical Efficacy Thesaurus, Application Domain, Technology Topic, Popular Technical Reports.
© 2025 PatSnap. All rights reserved.Legal|Privacy policy|Modern Slavery Act Transparency Statement|Sitemap|About US| Contact US: help@patsnap.com