Method for preparing composite reinforcement by taking plant fibers as template and application of composite reinforcement in metal-based composite material
A plant fiber and composite reinforcement technology, which is applied in metal material coating process, liquid chemical plating, coating, etc., can solve the problems of poor material toughness, low bonding force between reinforcement and metal matrix, and improve mechanical properties , good dispersibility and excellent binding performance
- Summary
- Abstract
- Description
- Claims
- Application Information
AI Technical Summary
Problems solved by technology
Method used
Examples
Embodiment 1
[0026] (1) Place 10 g of rice husk fiber, abaca fiber, and cotton fiber in deionized water, then add 0.026 g of 2-acrylamide-2-methylpropanesulfonic acid, and stir for 1 hour at a stirring speed of 1000 rpm. preparing a plant fiber dispersion; dissolving zinc acetate dihydrate in deionized water to obtain a metal salt solution, and adding the prepared metal salt solution to the plant fiber dispersion to obtain a mixed solution;
[0027] (2) Add sodium ethylenediamine tetraacetate solution and ammonia solution to the mixture at the same time at a rate of 1.15 L / h and 1.33 L / h, stir vigorously during the addition, and mix the reaction solution after the addition. Transfer to a reaction kettle, seal it, place it in an oven at 150°C for 10 hours, cool to room temperature after the reaction, filter the reaction solution, wash the filtered solid to neutral and then dry it to obtain an intermediate product A; wherein, the The addition of sodium edetate is 5% of the quality of zinc ac...
Embodiment 2
[0030] (1) Place 10 g of rice husk fiber, abaca fiber, and cotton fiber in deionized water, then add 0.075 g of 2-acrylamide-2-methylpropanesulfonic acid, and stir for 2 hours at a stirring speed of 1000 rpm, preparing a plant fiber dispersion; dissolving zinc acetate dihydrate in deionized water to obtain a metal salt solution, and adding the prepared metal salt solution to the plant fiber dispersion to obtain a mixed solution;
[0031] (2) Add sodium ethylenediamine tetraacetate solution and ammonia solution to the mixture at the same time at a rate of 1.15 L / h and 1.33 L / h, stir vigorously during the addition, and mix the reaction solution after the addition. Transfer to a reaction kettle, seal it, place it in an oven at 150°C for 10 hours, cool to room temperature after the reaction, filter the reaction solution, wash the filtered solid to neutral and then dry it to obtain an intermediate product A; wherein, the The addition of sodium edetate is 20% of the quality of zinc ...
Embodiment 3
[0034] (1) Put 10g of rice husk fiber, abaca fiber, and cotton fiber in deionized water, then add 0.033g of 2-acrylamide-2-methylpropanesulfonic acid, and stir at a stirring speed of 1000 rpm for 1.2h , to obtain a plant fiber dispersion; dissolving zinc acetate dihydrate in deionized water to obtain a metal salt solution, and adding the prepared metal salt solution to the plant fiber dispersion to obtain a mixed solution;
[0035] (2) Add sodium ethylenediamine tetraacetate solution and ammonia solution to the mixture at the same time at a rate of 1.15 L / h and 1.33 L / h, stir vigorously during the addition, and mix the reaction solution after the addition. Transfer to a reaction kettle, seal it, place it in an oven at 150°C for 10 hours, cool to room temperature after the reaction, filter the reaction solution, wash the filtered solid to neutral and then dry it to obtain an intermediate product A; wherein, the The addition of sodium edetate is 10% of the quality of zinc acetat...
PUM
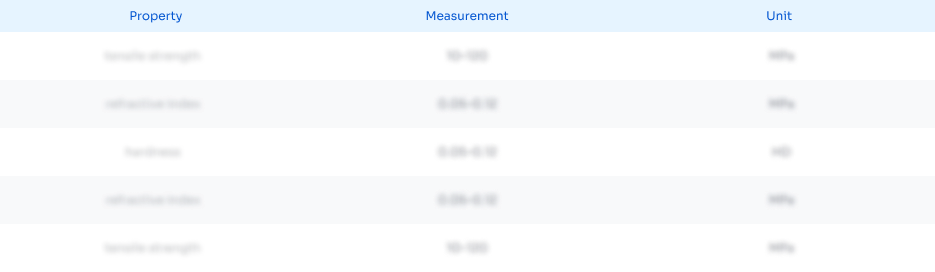
Abstract
Description
Claims
Application Information

- R&D Engineer
- R&D Manager
- IP Professional
- Industry Leading Data Capabilities
- Powerful AI technology
- Patent DNA Extraction
Browse by: Latest US Patents, China's latest patents, Technical Efficacy Thesaurus, Application Domain, Technology Topic, Popular Technical Reports.
© 2024 PatSnap. All rights reserved.Legal|Privacy policy|Modern Slavery Act Transparency Statement|Sitemap|About US| Contact US: help@patsnap.com