Asphalt mixture for color porous pavement upper layer and preparation method
A technology of asphalt mixture and permeable pavement, which is applied in the field of road engineering, can solve the problems of research on the mechanical properties of asphalt mixture with angular wear, unsatisfactory water permeability of permeable pavement, and easy fading of colored surface layer after service time, etc. Adhesion, good water permeability and road performance, and the effect of improving water damage resistance
- Summary
- Abstract
- Description
- Claims
- Application Information
AI Technical Summary
Problems solved by technology
Method used
Image
Examples
Embodiment 1
[0053] An asphalt mixture for the upper layer of colored permeable pavement, comprising the following raw materials, all in parts by weight: 3.12 parts of decolorized asphalt, 40.3 parts of aggregates of 3-5 mm, 51.3 parts of aggregates of 5-10 mm, and 1.93 parts of composite modified mineral powder Parts, 0.38 parts of granular lignin fiber, 2.89 parts of iron red.
[0054] The granular lignin fiber: the ash content is 17%, the pH value is 7.0, the oil absorption rate is 6.3 times, the thermal weight loss is 2%, and the moisture content is 2.3%.
[0055] The composite modified slag powder is: slaked lime powder and limestone slag powder are mixed, the slaked lime powder accounts for 40%, and the limestone slag powder accounts for 60%.
[0056] The preparation method of the above-mentioned permeable pavement upper layer asphalt mixture, the specific preparation method is as follows:
[0057] Step 1: Weigh the following components according to the weight of the above raw mater...
Embodiment 2
[0062] An asphalt mixture for the upper layer of colored permeable pavement, comprising the following raw materials, all in parts by weight: 3.42 parts of decolorized asphalt, 39.5 parts of aggregates of 3-5 mm, 52 parts of aggregates of 5-10 mm, and 1.95 parts of composite modified mineral powder parts, 0.4 parts of granular lignin fiber, and 2.9 parts of iron red.
[0063] The granular lignin fiber: the ash content is 17%, the pH value is 7.0, the oil absorption rate is 6.3 times, the thermal weight loss is 2%, and the moisture content is 2.3%.
[0064] The composite modified slag powder is: slaked lime powder and limestone slag powder are mixed, the slaked lime powder accounts for 40%, and the limestone slag powder accounts for 60%.
[0065] The preparation method of the above-mentioned permeable pavement upper layer bituminous mixture differs from Example 1 as follows:
[0066] In the step 2, all 3-5mm aggregates, 22% 5-10mm aggregates and granular lignin fibers were mixe...
Embodiment 3
[0068] An asphalt mixture for the upper layer of colored permeable pavement, comprising the following raw materials, all in parts by weight: 3.1 parts of decolorized asphalt, 39.82 parts of aggregates of 3-5 mm, 50.68 parts of aggregates of 5-10 mm, and 1.8 parts of composite modified mineral powder parts, 0.3 parts of granular lignin fiber, and 2.6 parts of iron red.
[0069] The granular lignin fiber: the ash content is 17%, the pH value is 7.0, the oil absorption rate is 6.3 times, the thermal weight loss is 2%, and the moisture content is 2.3%.
[0070] The composite modified slag powder is: slaked lime powder and limestone slag powder are mixed, and the proportion is: the slaked lime powder accounts for 35%, and the limestone slag powder accounts for 65%.
[0071] The preparation method of the above-mentioned permeable pavement upper layer bituminous mixture differs from Example 1 as follows:
[0072] In the step 2, all 3-5mm aggregates, 40% 5-10mm aggregates and granula...
PUM
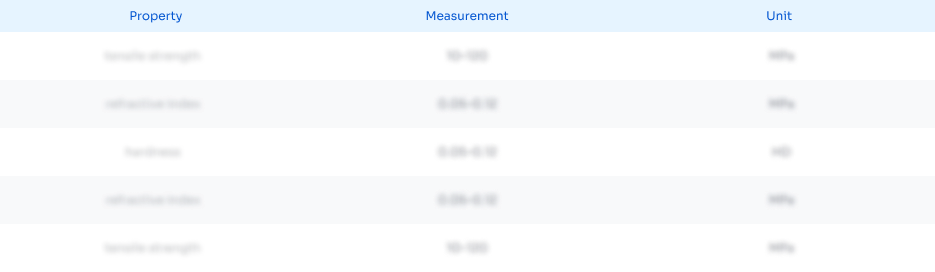
Abstract
Description
Claims
Application Information

- R&D
- Intellectual Property
- Life Sciences
- Materials
- Tech Scout
- Unparalleled Data Quality
- Higher Quality Content
- 60% Fewer Hallucinations
Browse by: Latest US Patents, China's latest patents, Technical Efficacy Thesaurus, Application Domain, Technology Topic, Popular Technical Reports.
© 2025 PatSnap. All rights reserved.Legal|Privacy policy|Modern Slavery Act Transparency Statement|Sitemap|About US| Contact US: help@patsnap.com