Biodegradable triblock copolymers and implantable medical devices made therefrom
A biodegradable and medical device technology, applied in medical science, conjugated synthetic polymer artificial filament, prosthesis, etc., can solve the problem of low efficiency of pure PLA filament
- Summary
- Abstract
- Description
- Claims
- Application Information
AI Technical Summary
Problems solved by technology
Method used
Image
Examples
Embodiment 1
[0159] Synthesis of ABA' triblock copolymers of poly(lactic acid)-[poly(lactic acid)-poly(trimethylene carbonate)]-poly(lactic acid)(PLA-[PLA-pTMC]-PLA) generally comprising 80 mol% PLA and 20 mol% pTMC and the B block [PLA-pTMC] is 0 mol% PLA and 100 mol% pTMC.
[0160] In the first polymerization stage, 5,000 g of trimethylene carbonate, 24.65 g of diethylene glycol and 0.02% stannous octoate were added to a clean and dry stainless steel conical vessel reactor equipped with two helical mixing blades, And dry mix under nitrogen atmosphere and initially at room temperature. The reactor temperature was raised to 180°C and the first stage reaction was monitored until complete formation of the B block, in this example 100% poly(TMC).
[0161] In the second polymerization stage, 28,261 g of dry lactide monomer and 0.02% stannous octoate were added to a stainless steel cone containing the B block from the first polymerization stage using a helical mixing blade and under a nitrogen...
Embodiment 2
[0163] Synthesis of ABA' triblock copolymers of poly(lactic acid)-[poly(lactic acid)-poly(trimethylene carbonate)]-poly(lactic acid)(PLA-[PLA-pTMC]-PLA), 80 moles overall % PLA and 20 mol% pTMC, where the B block [PLA-pTMC] is 15 mol% PLA and 85 mol% pTMC.
[0164] In the first polymerization stage, 5,000 g of trimethylene carbonate, 1247 g of dry L-lactide monomer, 2.75 g of diethylene glycol and 2.90 g of stannous octoate were added to a clean and dry Stainless steel conical vessel reactor with mixing blades, and dry mix under nitrogen atmosphere and initially at room temperature. The reactor temperature was raised to 180°C and the first stage reaction was monitored until complete formation of the B block, in this example a random copolymer comprising 15 mole % PLA and 85 mole % pTMC.
[0165] In the second polymerization stage, 27,014 g of dry lactide monomer was added to a stainless steel conical vessel reactor comprising the B block from the first polymerization stage us...
Embodiment 3
[0167] Each of the ABA' triblock copolymers formed in Examples 1 and 2 above, as well as pure PLA alone and several additional PLA / TMC triblocks with various total mole percent and / or midblock mole percent Segment copolymers are extruded to form filaments of various diameters. The tensile strength and molar mass of the polymeric filaments were tested in vitro to provide the degradation profile of each filament. Specifically, the tensile strength retention pattern at 50°C and the molar mass retention pattern at 50°C were investigated. Degradation was performed at 50°C in 1 / 1 molar phosphate buffer, pH=7.4. Degradation and measurement of tensile strength and molar mass are according to ISO 13781:1997 "Poly(L-lactide) resins and fabricated forms for surgical implants - In vitro degradation test (Poly(L-lactide) resins and fabricated forms for surgical implants-in vitrodegradation testing)". The terms "retention of tensile strength at 50°C" and "retention of molar mass at 50°C"...
PUM
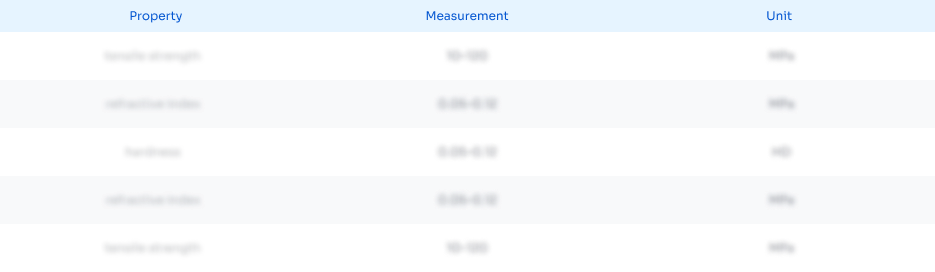
Abstract
Description
Claims
Application Information

- Generate Ideas
- Intellectual Property
- Life Sciences
- Materials
- Tech Scout
- Unparalleled Data Quality
- Higher Quality Content
- 60% Fewer Hallucinations
Browse by: Latest US Patents, China's latest patents, Technical Efficacy Thesaurus, Application Domain, Technology Topic, Popular Technical Reports.
© 2025 PatSnap. All rights reserved.Legal|Privacy policy|Modern Slavery Act Transparency Statement|Sitemap|About US| Contact US: help@patsnap.com