Low-temperature-resistant and wear-resistant non-yellowing polyurethane resin and ultrafine fiber synthetic leather prepared from same
A polyurethane resin, non-yellowing technology, applied in the field of polyurethane resin and non-yellowing polyurethane, can solve the problems of precipitation, poor weather resistance and aging resistance of polyurethane, and achieve reduced crystallinity, excellent aging resistance, and avoidance of The effect of reducing the low temperature folding resistance
- Summary
- Abstract
- Description
- Claims
- Application Information
AI Technical Summary
Problems solved by technology
Method used
Examples
Embodiment 1
[0045] Polycarbonate diol (UH-200) 130g (molecular weight 2000), poly 3-methyltetrahydrofuran diol 15g (molecular weight 2000), dihydroxy silicone oligomer (Silok8866) 20g (molecular weight 4500), hydrogenated terminal Mix 20g of hydroxyl polybutadiene (molecular weight: 2000) and 100g of N,N dimethylformamide at 55°C; then add 44.1g of 4,4'-dicyclohexylmethane diisocyanate, raise the temperature to 70°C, and react for 0.5 hours ,
[0046] Add 0.01g organic bismuth catalyst, raise the temperature to 110°C, and react for 3 hours;
[0047] Add 251.5g of N,N dimethylformamide and 221g of toluene, cool down to below 50°C, add 17.6g of 4,4-diaminodicyclohexylmethane dropwise to increase viscosity;
[0048] When the viscosity reaches 80PaS / 25°C, stop the dropwise addition, add 0.8g of single-ended aminosiloxane to terminate the reaction, and keep it warm for 1 hour to obtain the non-yellowing polyurethane resin with a mass solid content of 30%.
Embodiment 2
[0050] Polycarbonate diol (UH-200) 110g (molecular weight 2000), dihydroxy silicone oligomer (Silok8866) 20g (molecular weight 4500), hydrogenated hydroxyl-terminated polybutadiene 30g (molecular weight 2000) and N, N two Mix 100g of methylformamide at 50°C; then add 58.2g of 4,4'-dicyclohexylmethane diisocyanate, raise the temperature to 70°C, and react for 0.5 hours.
[0051] Add 0.02g organic bismuth catalyst, raise the temperature to 100°C, and react for 3 hours;
[0052] Add 249g of N,N dimethylformamide and 233g of toluene, lower the temperature to below 50°C, and add 31g of 4,4-diaminodicyclohexylmethane dropwise to increase the viscosity;
[0053] When the viscosity reaches 100PaS / 25°C, stop the dropwise addition, add 1g of single-ended aminosiloxane to terminate the reaction, and keep it warm for 1 hour to obtain the non-yellowing polyurethane resin with a mass solid content of 30%.
Embodiment 3
[0055] Polycarbonate diol (UH-200) 130g (molecular weight 2000), poly 3-methyltetrahydrofuran diol 30g (molecular weight 2000), dihydroxy silicone oligomer (Silok8866) 30g (molecular weight 4500), hydrogenated terminal 20g of hydroxyl polybutadiene (molecular weight 2000) and 100g of N,N dimethylformamide were mixed at 50°C; then 42.2g of isophorone diisocyanate was added, the temperature was raised to 70°C, and the reaction was carried out for 0.5 hours.
[0056] Add 0.04 organic bismuth catalyst, raise the temperature to 90°C, and react for 2 hours;
[0057]Add 282g of N,N dimethylformamide and 241g of toluene, cool down to below 50°C, add 16.1g of isophoronediamine dropwise to increase the viscosity;
[0058] When the viscosity reaches 120PaS / 25°C, stop the dropwise addition, add 1.8g of single-ended aminosiloxane to terminate the reaction, and keep it warm for 1 hour to obtain the non-yellowing polyurethane resin with a mass solid content of 30%.
PUM
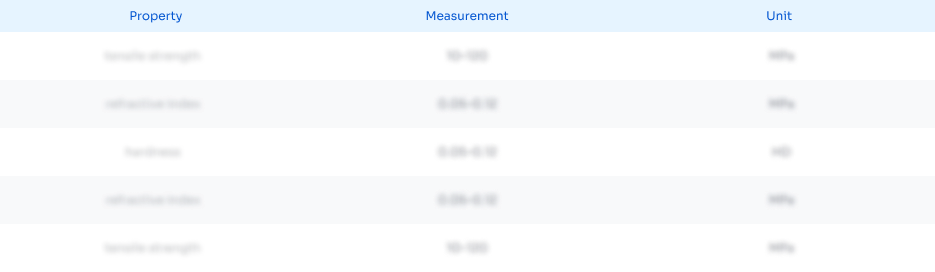
Abstract
Description
Claims
Application Information

- Generate Ideas
- Intellectual Property
- Life Sciences
- Materials
- Tech Scout
- Unparalleled Data Quality
- Higher Quality Content
- 60% Fewer Hallucinations
Browse by: Latest US Patents, China's latest patents, Technical Efficacy Thesaurus, Application Domain, Technology Topic, Popular Technical Reports.
© 2025 PatSnap. All rights reserved.Legal|Privacy policy|Modern Slavery Act Transparency Statement|Sitemap|About US| Contact US: help@patsnap.com