Preparation method of waste gas purifying catalyst
A technology for exhaust gas purification and catalyst, applied in catalyst activation/preparation, physical/chemical process catalysts, chemical instruments and methods, etc., can solve the problems of sulfur poisoning and catalyst performance degradation, and achieve the goal of preventing sulfur poisoning and enhancing sulfur resistance. Effect
- Summary
- Abstract
- Description
- Claims
- Application Information
AI Technical Summary
Problems solved by technology
Method used
Image
Examples
Embodiment 1
[0027] Embodiment 1: Weigh 68g of pseudoboehmite (AlOOH 0.5H 2 (2) and 21g cerium nitrate hexahydrate, then weighed 8.04g copper nitrate (the percentage value is 5% by copper oxide mass and carrier mass after loading) and 0.29g platinum nitrate (by the ratio of platinum oxide mass and carrier mass after loading) The percentage value is 0.3%); add 500ml of deionized water and 10ml of dimethyl sulfoxide to the carrier and metal component precursor, shake well, add an appropriate amount of sodium hydroxide aqueous solution to adjust the pH to 7; condense and stir at 80°C 10 hours; use a rotary evaporator to spin-dry; place in an oven to dry at 120°C overnight; after grinding evenly, put it in a muffle furnace and bake at 550°C for 4 hours to obtain 1-Cu-Pt / CeO 2 -Al 2 o 3 , denoted as catalyst 1.
Embodiment 2
[0028] Embodiment 2: Weigh 68g of pseudoboehmite (AlOOH 0.5H 2 (2) and 54g cerium nitrate hexahydrate, then weighed 11.14g copper nitrate (the percentage value of copper oxide mass and carrier mass after loading is 5%) and 0.79g platinum nitrate (the percentage value of platinum oxide mass and carrier mass after loading 0.6%); add 470ml of deionized water and 40ml of dimethyl sulfoxide to the carrier and metal component precursor, shake well, add an appropriate amount of sodium hydroxide aqueous solution to adjust the pH to 8; condense and stir at 90°C for 16 hours ;Use a rotary evaporator to spin-dry; put it in an oven at 120°C for overnight drying; after grinding evenly, put it in a muffle furnace and bake it at 650°C for 6 hours to obtain 2-Cu-Pt / CeO 2 -Al 2 o 3 , denoted as Catalyst 2.
Embodiment 3
[0032] Example 3: The only difference between this embodiment and Example 1 is that only 510ml of water is added and no dimethyl sulfoxide is added, and the others are the same as in Example 1 to obtain 3-Cu-Pt / CeO 2 -Al 2 o 3 , denoted as catalyst 6.
[0033] Adopt following experiment verification effect of the present invention:
[0034]The prepared catalyst was pressed into tablets, ground, and sieved to collect 40-60 mesh catalyst particles, and 0.2 g of catalyst was filled in the middle of a fixed-bed reactor (quartz tube reactor with a diameter of 6.0 mm). Then, the saturated steam of DMDS (dimethyl disulfide) was introduced into the main pipeline by nitrogen bubbling method, and mixed with nitrogen and air. Finally, the oxidation reaction takes place in the fixed bed reactor. The reaction process conditions are as follows: under normal pressure, the reaction temperature rises from 100°C to 550°C, the DMDS concentration is 1000ppm, and the volumetric space velocity ...
PUM
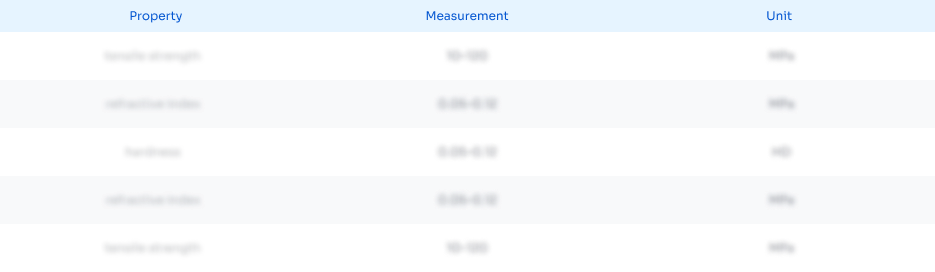
Abstract
Description
Claims
Application Information

- R&D
- Intellectual Property
- Life Sciences
- Materials
- Tech Scout
- Unparalleled Data Quality
- Higher Quality Content
- 60% Fewer Hallucinations
Browse by: Latest US Patents, China's latest patents, Technical Efficacy Thesaurus, Application Domain, Technology Topic, Popular Technical Reports.
© 2025 PatSnap. All rights reserved.Legal|Privacy policy|Modern Slavery Act Transparency Statement|Sitemap|About US| Contact US: help@patsnap.com