Method for processing silicon carbide microwave heating medium kiln furniture by using powdered quartz
A microwave heating and silicon carbide technology, which is applied in the field of kiln furniture, can solve unseen problems, and achieve the effects of improving heating effect, increasing power consumption and rapid heating
- Summary
- Abstract
- Description
- Claims
- Application Information
AI Technical Summary
Problems solved by technology
Method used
Examples
Embodiment 1
[0030] Step 1: Mix the raw materials of powdered quartz and carbon powder in a molar ratio of 0.7:1, mechanically stir and mix (stirring speed 100r / min, stirring time 24h), put it into a vacuum sintering furnace for heating, heat to 1850°C, Keep warm for 10 hours, and then sinter to produce cubic silicon carbide powder, which is gray-black;
[0031] Step 2: Put the silicon carbide powder in step 1 into a microwave heating furnace and heat it to 800°C to oxidize the unreacted carbon powder into carbon dioxide to obtain light green cubic silicon carbide powder;
[0032] Step 3: Mix the cubic silicon carbide powder collected in step 2 with absolute ethanol in a ratio of 100g:10ml to form a slurry, and stir through a wet mill (stirring speed 30r / min, stirring time 24h), and then Extrude the mixed mud into a honeycomb silicon carbide body through an extrusion molding machine;
[0033] Step 4: Put the honeycomb silicon carbide body obtained in Step 3 into a microwave tunnel kiln fo...
Embodiment 2
[0038] Step 1: Mix the raw materials of powdered quartz and carbon powder in a molar ratio of 0.7:1, mechanically stir and mix (stirring speed 300r / min, stirring time 10h), put it into a resistance furnace for heating, heat to 1800°C, and keep warm After 20 hours, sintering produces cubic silicon carbide powder, which is gray-black;
[0039] Step 2: Put the silicon carbide powder in step 1 into a microwave heating furnace and heat it to 800°C to oxidize the unreacted carbon powder into carbon dioxide to obtain light green cubic silicon carbide powder;
[0040] Step 3: Mix the cubic silicon carbide powder collected in step 2 with absolute ethanol in a ratio of 100g:10ml to form a slurry, and stir through a wet mill (stirring speed 60r / min, stirring time 10h), and then Extrude the mixed mud into a single-walled tubular silicon carbide billet through an extrusion molding machine;
[0041] Step 4: Put the single-walled tubular silicon carbide green body obtained in Step 3 into a ...
Embodiment 3
[0046] Step 1: Mix the raw materials of powdered quartz and carbon powder in a molar ratio of 0.7:1, mechanically stir and mix (stirring speed 200r / min, stirring time 15h), put it into an intermediate frequency induction furnace for heating, and heat it to 1900°C. Keep warm for 10 hours, and then sinter to produce cubic silicon carbide powder, which is gray-black;
[0047] Step 2: Put the silicon carbide powder in step 1 into a microwave heating furnace and heat it to 800°C to oxidize the unreacted carbon powder into carbon dioxide to obtain light green cubic silicon carbide powder;
[0048] Step 3: Mix the cubic silicon carbide powder collected in step 2 with absolute ethanol in a ratio of 100g:10ml to form a slurry, and stir through a wet mill (stirring speed 60r / min, stirring time 10h), and then Extrude the mixed mud into a honeycomb silicon carbide body through an extrusion molding machine;
[0049] Step 4: Put the honeycomb silicon carbide body obtained in Step 3 into a ...
PUM
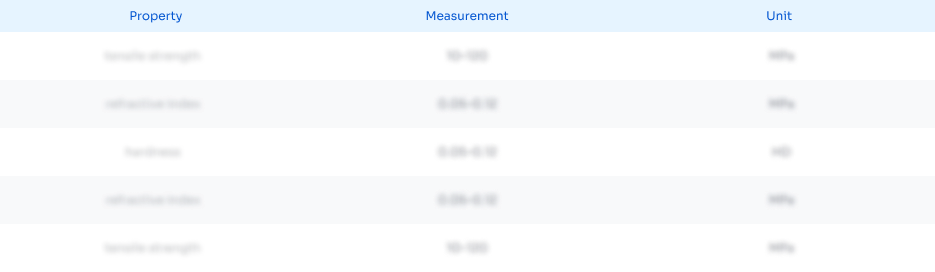
Abstract
Description
Claims
Application Information

- Generate Ideas
- Intellectual Property
- Life Sciences
- Materials
- Tech Scout
- Unparalleled Data Quality
- Higher Quality Content
- 60% Fewer Hallucinations
Browse by: Latest US Patents, China's latest patents, Technical Efficacy Thesaurus, Application Domain, Technology Topic, Popular Technical Reports.
© 2025 PatSnap. All rights reserved.Legal|Privacy policy|Modern Slavery Act Transparency Statement|Sitemap|About US| Contact US: help@patsnap.com