A kind of methanol oxidation to formaldehyde iron molybdenum catalyst and its preparation and application
A catalyst and oxidation technology, applied in the direction of physical/chemical process catalysts, metal/metal oxide/metal hydroxide catalysts, carbon-based compound preparation, etc., can solve the problem of insoluble wastewater and waste gas, environmental protection, high catalyst preparation costs, etc. question
- Summary
- Abstract
- Description
- Claims
- Application Information
AI Technical Summary
Problems solved by technology
Method used
Image
Examples
Embodiment 1
[0019] First, 56 grams of iron powder is added to an excess mass concentration of 20% p-toluenesulfonic acid solution to generate iron p-toluenesulfonate and hydrogen; followed by adding a mass concentration of 20% heptamolybdic acid aqueous solution and Iron p-toluenesulfonate reacts to generate iron molybdate and p-toluenesulfonic acid, and iron molybdate precipitation, as the main active component of iron-molybdenum catalyst, can be separated from regenerated p-toluenesulfonic acid by simple filtration; / Fe=2.0 The generated ferric molybdate and heptamolybdic acid aqueous solution with a mass concentration of 20% are beaten and mixed, and the obtained slurry is aged at 90°C for 12h; then filtered to obtain a filter cake; the filter cake is dried at 80°C, powdered Purified, molded, and calcined at 400°C for 24 hours to obtain an iron-molybdenum catalyst (MoO 3 -Fe 2 (MoO 4 ) 3 ).
Embodiment 2
[0024] Embodiment 2: different organic acid species (citric acid)
[0025] First, 56 grams of iron powder is added to excess mass concentration of 15% citric acid solution to generate ferric citrate and hydrogen; then add heptamolybdic acid aqueous solution with a mass concentration of 40% to react with ferric citrate according to the stoichiometric ratio Ferric molybdate and citric acid are generated, and ferric molybdate precipitation is the main active component of the iron-molybdenum catalyst, which can be separated from the regenerated citric acid by simple filtration; Mix it with a 40% heptamolybdic acid aqueous solution, and age the obtained slurry at 90°C for 12 hours; then filter to obtain a filter cake; the filter cake is dried at 80°C, pulverized, shaped, and roasted at 400°C for 24 hours to obtain Iron molybdenum catalyst (MoO 3 -Fe 2 (MoO 4 ) 3 ).
Embodiment 3
[0026] Embodiment 3: different organic acid types (fumaric acid)
[0027] First, 56 grams of iron powder is added to an excessive mass concentration of 15% fumaric acid solution to generate iron fumarate and hydrogen; then add a mass concentration of 60% heptamolybdic acid aqueous solution and fumaric acid Iron molybdate reacts to generate iron molybdate and fumaric acid, and iron molybdate precipitation is the main active component of the iron-molybdenum catalyst, which can be separated from the regenerated fumaric acid by simple filtration; then the final product Mo / Fe=2.0 will The generated ferric molybdate is beaten and mixed with an aqueous solution of heptamolybdic acid with a mass concentration of 60%, and the obtained slurry is aged at 90°C for 12 hours; then filtered to obtain a filter cake; Roasting 24h obtains the iron-molybdenum catalyst (MoO 3 -Fe 2 (MoO 4 ) 3 ).
PUM
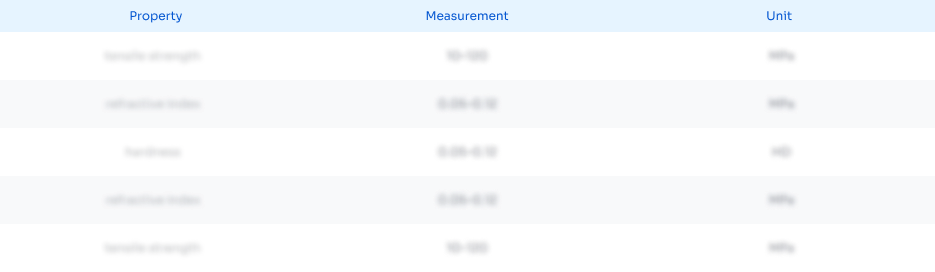
Abstract
Description
Claims
Application Information

- R&D
- Intellectual Property
- Life Sciences
- Materials
- Tech Scout
- Unparalleled Data Quality
- Higher Quality Content
- 60% Fewer Hallucinations
Browse by: Latest US Patents, China's latest patents, Technical Efficacy Thesaurus, Application Domain, Technology Topic, Popular Technical Reports.
© 2025 PatSnap. All rights reserved.Legal|Privacy policy|Modern Slavery Act Transparency Statement|Sitemap|About US| Contact US: help@patsnap.com