Beneficiation method for efficiently recovering copper from copper smelting slags
A technology for copper smelting slag and beneficiation method, which is applied in the direction of solid separation, etc., can solve the problems of poor adaptability and large fluctuation of copper flotation index, and achieves the effects of stable operation, improved comprehensive utilization of resources and advanced technology.
- Summary
- Abstract
- Description
- Claims
- Application Information
AI Technical Summary
Problems solved by technology
Method used
Image
Examples
Embodiment 1
[0023] ① Steps: coarse grinding + classification, copper smelting slag 1 is fed into coarse grinding 2, and the ore discharge product 3 of coarse grinding 2 enters classification 4, and overflow product 5 and grit 6 are obtained, and grit 6 returns to coarse grinder 2 Operation, the fineness of the overflow product 5 is -0.074mm, accounting for 58.62%;
[0024] ② Step: re-election in the spiral chute, adding water to the overflow product 5 to adjust the mass concentration of the pulp to 28.81%, and then feeding it into the re-election 7 operation in the spiral chute to obtain the gravity-selected copper concentrate 8 and the gravity-selected tailings 9;
[0025] ③ Step: fine grinding, feeding the gravity separation tailings 9 into the fine grinding 10, and the fineness of the discharge product 11 of the fine grinding 10 is -0.045mm, accounting for 81.85%;
[0026] ④ Step: Priority flotation, add Z-200 agent 80g / t, isopentyl xanthate 20g / t, terpineol oil 20g / t in sequence in pr...
Embodiment 2
[0034] ① The fineness of the overflow product 5 in the step is -0.074mm, accounting for 61.37%;
[0035] ② In the step, the mass concentration of the pulp after adding water to the overflow product 5 is 29.32%;
[0036] ③The fineness of the ore discharge product 11 in the step is -0.045mm and accounts for 84.53%;
[0037]④, ⑤, and ⑥ steps are only different in the amount of the following medicaments in Example 1, and all the other are the same as in Example 1, being respectively: ④ the consumption of medicaments in the step is: Z-200 medicament 90g / t, isoamyl xanthate 30g / t, Terpineol oil 30g / t; ⑤The dosage of medicament in the step is: sodium sulfide 650 / t, isopentyl xanthate 40g / t, butyl ammonium black medicine 20g / t, terpineol oil 15g / t; ⑥The amount of medicament in the step The dosage is: sodium sulfide 320g / t, isopentyl xanthate 20g / t, butylammonium black medicine 10g / t;
[0038] 7. step is identical with embodiment 1;
[0039] The processing of middle ore is identical...
PUM
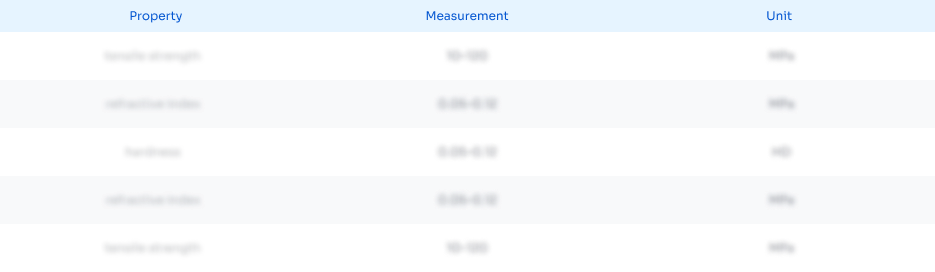
Abstract
Description
Claims
Application Information

- R&D
- Intellectual Property
- Life Sciences
- Materials
- Tech Scout
- Unparalleled Data Quality
- Higher Quality Content
- 60% Fewer Hallucinations
Browse by: Latest US Patents, China's latest patents, Technical Efficacy Thesaurus, Application Domain, Technology Topic, Popular Technical Reports.
© 2025 PatSnap. All rights reserved.Legal|Privacy policy|Modern Slavery Act Transparency Statement|Sitemap|About US| Contact US: help@patsnap.com