Adsorber for cleaning exhaust gases and associated method
An adsorber and exhaust gas technology, which is applied in chemical instruments and methods, separation methods, gas treatment, etc., can solve problems such as inability to clean up, operation interruption, and increased pressure loss, so as to save time and cost, improve equipment availability, and absorber compact effect
- Summary
- Abstract
- Description
- Claims
- Application Information
AI Technical Summary
Problems solved by technology
Method used
Image
Examples
Embodiment Construction
[0051] figure 1 Shown is an adsorber 1a according to the invention for exhaust gas purification, which comprises the following components: a gas distribution floor 2; a discharge device 3; a bulk material area 4 arranged above the gas distribution floor 2; A discharge device 5 above the bulk material area 4 ; a store room 6 arranged above the discharge device 5 ; several nozzles 7 extending into the bulk material area 4 and having at least one opening that is horizontal and arranged parallel to each other. contains SO x and NO x , At the same time, the exhaust gas that may also contain HCl, dioxin, furan, heavy metals and dust passes through the gas distribution bottom plate 2 of the adsorber 1a, and is transported from below to the adsorber 1a in a substantially uniform distribution, and flows from bottom to top Through bulk zone 4 of adsorber 1a. The bulk material zone 4 is filled with activated carbon 8 as adsorbent and / or absorbent and has a lower zone 9 and an upper zo...
PUM
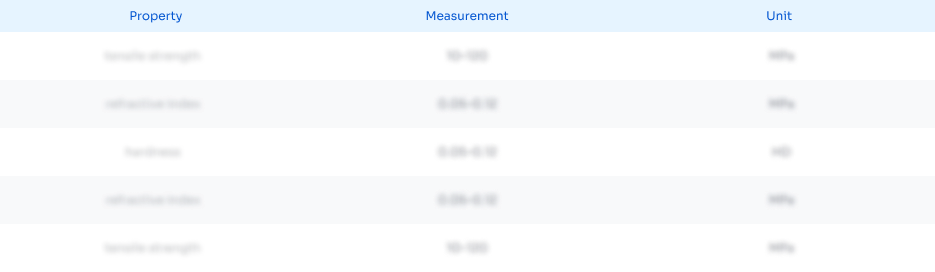
Abstract
Description
Claims
Application Information

- Generate Ideas
- Intellectual Property
- Life Sciences
- Materials
- Tech Scout
- Unparalleled Data Quality
- Higher Quality Content
- 60% Fewer Hallucinations
Browse by: Latest US Patents, China's latest patents, Technical Efficacy Thesaurus, Application Domain, Technology Topic, Popular Technical Reports.
© 2025 PatSnap. All rights reserved.Legal|Privacy policy|Modern Slavery Act Transparency Statement|Sitemap|About US| Contact US: help@patsnap.com