A kind of preparation method of ozone decomposition catalyst in high-humidity exhaust gas
A technology of ozone decomposition and catalyst, which is applied in molecular sieve catalysts, separation methods, chemical instruments and methods, etc. It can solve the problems of the decrease of ozone catalytic degradation efficiency and the catalyst's inability to withstand high humidity exhaust gas, so as to save power energy consumption and ensure catalytic decomposition effect, the effect of increasing the load
- Summary
- Abstract
- Description
- Claims
- Application Information
AI Technical Summary
Problems solved by technology
Method used
Image
Examples
preparation example Construction
[0024] A method for preparing an ozone decomposition catalyst in a high-humidity exhaust gas, comprising the following steps:
[0025] (1) The molar ratio of ferric nitrate, manganese nitrate, copper nitrate and silver nitrate is 1:(0.1~1):(0.1~1):(0.1~0.5) deionized water, the amount of deionized water and the ferric nitrate The molar ratio is (80-200):1, and it is configured as an immersion liquid. Add ZSM-5 molecular sieve powder with a silicon-alumina ratio of 50-300 to the impregnation solution, and the molecular sieve dosage is 1-2 times the mass of iron nitrate, manganese nitrate, copper nitrate and silver nitrate, and ultrasonically disperse. Place on a shaker and soak for 2 to 24 hours. filter. Transfer to an oven and dry at 60-100°C for 2-6 hours. Transfer to a muffle furnace and bake at 400-550°C for 2-6 hours. Grind into powder and pass through a 200-mesh sieve. The supported molecular sieve powder was obtained.
[0026] (2) Dissolve ethyl orthosilicate and a...
Embodiment 1
[0030] Ferric nitrate, manganese nitrate, copper nitrate and silver nitrate were dissolved in 80moL of deionized water at the rate of 1moL:1moL:1moL:0.5moL to prepare an immersion solution. 780 g of ZSM-5 molecular sieve powder with a silicon-alumina ratio of 300 was added to the impregnation solution, and ultrasonically dispersed. Place on shaker and soak for 24 hours. Transfer to an oven and dry at 80°C for 4 hours. Transfer to a muffle furnace and bake at 400°C for 2 hours. Grind into powder and pass through a 200-mesh sieve. The supported molecular sieve powder was obtained.
[0031]Ethyl orthosilicate and n-propyl triethoxysilane are dissolved in ethanol, and the dosages of ethyl orthosilicate, n-propyl triethoxysilane and ethanol are 1moL:0.1moL:5moL. Rapid stirring, dropwise addition of 0.3 mol / L dilute hydrochloric acid to adjust pH to 2, and stirring at room temperature for 12 hours. 10.4 g of the above-obtained supported molecular sieve powder was added, stirred...
Embodiment 2
[0043] Ferric nitrate, manganese nitrate, copper nitrate, and silver nitrate were dissolved in 200 moL of deionized water at the rate of 1moL:0.1moL:0.1moL:0.1moL to prepare an immersion solution. 591 g of ZSM-5 molecular sieve powder with a silicon-alumina ratio of 50 was added to the impregnation solution, and ultrasonically dispersed. Place on shaker and soak for 24 hours. filter. Transfer to an oven and dry at 80°C for 2 hours. Transfer to a muffle furnace and bake at 550°C for 2 hours. Grind into powder and pass through a 200-mesh sieve. The supported molecular sieve powder was obtained.
[0044] Ethyl orthosilicate and n-octyltriethoxysilane are dissolved in ethanol, and the molar ratio of ethyl orthosilicate, n-octyltriethoxysilane and ethanol is 1:0.5:10. Rapid stirring, dropwise addition of 0.3 mol / L hydrochloric acid to adjust pH to 4, and stirring at room temperature for 24 hours. 42 g of the above-obtained supported molecular sieve powder was added, stirred r...
PUM
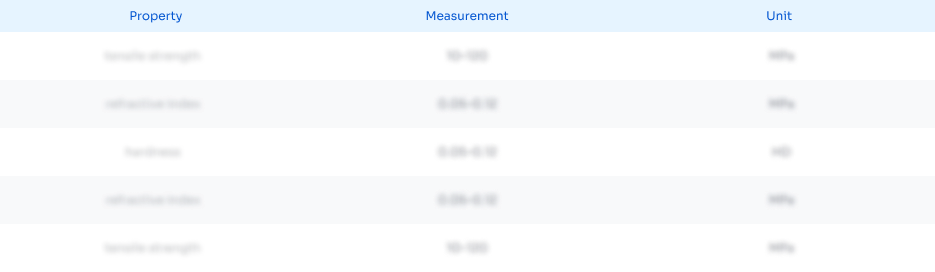
Abstract
Description
Claims
Application Information

- Generate Ideas
- Intellectual Property
- Life Sciences
- Materials
- Tech Scout
- Unparalleled Data Quality
- Higher Quality Content
- 60% Fewer Hallucinations
Browse by: Latest US Patents, China's latest patents, Technical Efficacy Thesaurus, Application Domain, Technology Topic, Popular Technical Reports.
© 2025 PatSnap. All rights reserved.Legal|Privacy policy|Modern Slavery Act Transparency Statement|Sitemap|About US| Contact US: help@patsnap.com