End surface driving film clamping device
A film and end face technology, applied in the field of hypersonic test equipment, can solve the problem of large radial space of the drive device, and achieve the effect of reducing the occupation of radial space and small volume
- Summary
- Abstract
- Description
- Claims
- Application Information
AI Technical Summary
Problems solved by technology
Method used
Image
Examples
Embodiment 1
[0032] Such as figure 1 , 2 As shown, the end-face driven clamping device of the present invention includes a driving section 1, a rotary nut 2, a diaphragm 3, a clamping ring 4, a transition nut 5, a driven section 6, a trunnion 7, a double ear support 8, a single ear Support 9 and oil cylinder 10;
[0033] Driving section 1: It is the upstream pipe section of the shock tube, and the inside is a cylindrical cavity. During the test, the cavity is filled with high-pressure driving gas. The right end of the driving section 1 is provided with an external thread, which is threaded with the internal thread on the left side of the rotary nut 2. ;
[0034] Rotary nut 2: connects the upstream pipe section and the downstream pipe section of the shock tube, the two ends of the inner hole are respectively processed with internal threads, the left internal thread is connected with the external thread at the right end of the driving section 1, and the right internal thread is connected w...
PUM
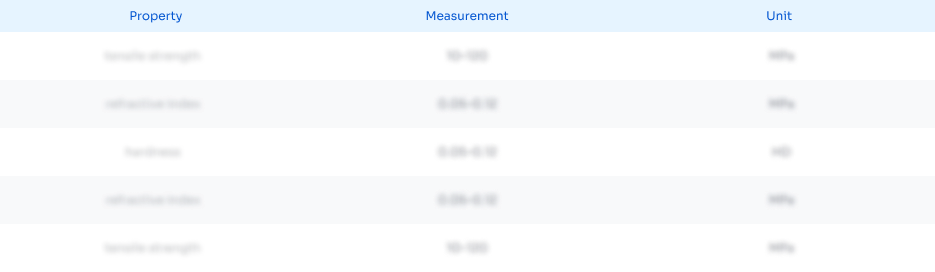
Abstract
Description
Claims
Application Information

- R&D
- Intellectual Property
- Life Sciences
- Materials
- Tech Scout
- Unparalleled Data Quality
- Higher Quality Content
- 60% Fewer Hallucinations
Browse by: Latest US Patents, China's latest patents, Technical Efficacy Thesaurus, Application Domain, Technology Topic, Popular Technical Reports.
© 2025 PatSnap. All rights reserved.Legal|Privacy policy|Modern Slavery Act Transparency Statement|Sitemap|About US| Contact US: help@patsnap.com