Modified raw soil material for 3D printing and preparation method of modified raw soil material
A 3D printing and permanent soil technology, applied in the direction of additive processing, etc., can solve the problems of low strength, low flexural and shear strength, etc., to improve early strength and crack resistance, good cold resistance, economic benefits and Significant social benefits
- Summary
- Abstract
- Description
- Claims
- Application Information
AI Technical Summary
Problems solved by technology
Method used
Image
Examples
Embodiment 1
[0028] A preparation method of modified raw soil material for 3D printing, comprising the following steps:
[0029] Step 1: Mix 0.059% polyvinyl butyral, 0.042% calcium lignosulfonate and water at a temperature of 42°C under sealed conditions, and stir for 3.5 hours to obtain a modified material for later use. Among them, the water content of the modified material is 72%.
[0030] Step 2: Mix 0.153% lipid polycarboxylate superplasticizer, 0.08% organic silicon, 0.047% calcium oxide and water to obtain an auxiliary agent mixture for future use.
[0031] Step 3, mix 88.182% raw soil, 0.476% rice straw (rice straw), 0.106% alum, 0.532% gypsum, 1.144% lime, 1.039% rapid hardening Portland cement, and 0.464% aluminate cement to obtain a mixture ,spare.
[0032] Step 4, first mix the modified material and the auxiliary agent mixture, stir once for 25 minutes, then add the mixture, 0.402% glutinous rice pulp and water, and stir for the second time (use cement mortar mixer for the s...
Embodiment 2
[0034] A preparation method of modified raw soil material for 3D printing, comprising the following steps:
[0035] Step 1: Mix 0.059% polyvinyl butyral, 0.042% calcium lignosulfonate and water at a temperature of 45°C under sealed conditions, and stir for 3 hours to obtain a modified material, which is set aside. Wherein, the water content of the modified material is 70%.
[0036] Step 2: Mix 0.153% naphthalene-based high-efficiency water reducer, 0.08% silicone, 0.047% early-strength agent and water to obtain a mixture of additives for later use. Wherein, the early strength agent comprises calcium oxide and potassium bicarbonate with a mass ratio of 1:2.
[0037] Step 3: Mix 87.359% raw soil, 0.476% straw, 0.106% alum, 0.913% gypsum, 1.144% lime, 1.039% rapid hardening portland cement, and 0.824% aluminate cement to obtain a mixture for use.
[0038] Step 4, first mix the modified material and the auxiliary agent mixture, stir once for 25 minutes, then add the mixture, 0.4...
Embodiment 3
[0040] A preparation method of modified raw soil material for 3D printing, comprising the following steps:
[0041] Step 1: Mix 0.076% polyvinyl butyral, 0.065% calcium lignosulfonate and water at a temperature of 40°C under sealed conditions, and stir for 4 hours to obtain a modified material, which is set aside. Wherein, the water content of the modified material is 75%.
[0042] Step 2: Mix 0.186% ether-based polycarboxylate water reducer, 0.104% silicone, 0.054% triethanolamine and water to obtain an auxiliary agent mixture for later use.
[0043] Step 3: Mix 88.81% raw soil, 0.476% straw, 0.091% alum, 0.429% gypsum, 1.152% lime, 1.22% rapid hardening Portland cement, and 0.625% aluminate cement to obtain a mixture for use.
[0044]Step 4, first mix the modified material and the auxiliary agent mixture, stir once for 25 minutes, then add the mixture, 0.43% glutinous rice pulp and water, and stir for the second time (use cement mortar mixer for the second stirring, and sti...
PUM
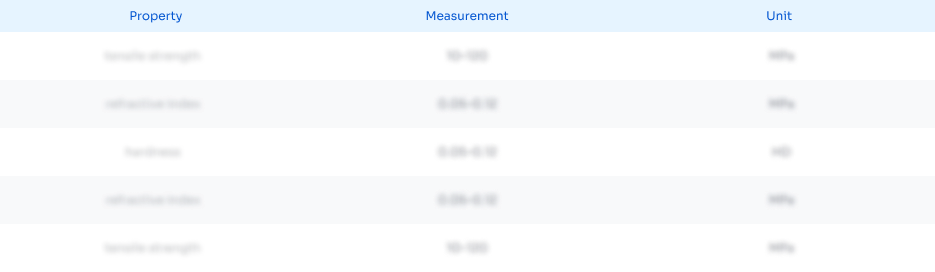
Abstract
Description
Claims
Application Information

- R&D
- Intellectual Property
- Life Sciences
- Materials
- Tech Scout
- Unparalleled Data Quality
- Higher Quality Content
- 60% Fewer Hallucinations
Browse by: Latest US Patents, China's latest patents, Technical Efficacy Thesaurus, Application Domain, Technology Topic, Popular Technical Reports.
© 2025 PatSnap. All rights reserved.Legal|Privacy policy|Modern Slavery Act Transparency Statement|Sitemap|About US| Contact US: help@patsnap.com