Method for preparing amorphous silicon/carbon composite material
A carbon composite material and amorphous silicon technology, applied in the preparation/purification of carbon, silicon compounds, chemical instruments and methods, etc., can solve problems such as environmental pollution, expensive and dangerous, achieve optimized preparation process, and be easy for industrial implementation , excellent cycle stability and rate performance
- Summary
- Abstract
- Description
- Claims
- Application Information
AI Technical Summary
Problems solved by technology
Method used
Image
Examples
Embodiment 1
[0029] Under the condition of nitrogen atmosphere protection, the magnesium silicide and lithium carbonate with a mass ratio of 2:1 were ball-milled at a speed of 500r / min with a ball-to-material ratio of 30:1 for 24 hours, and then the ball-milled uniform mixture was transferred to a closed reactor ; Then rise to 300°C at a heating rate of 5°C / min for 2 hours and then cool to room temperature;
[0030] The product was sequentially soaked in 1M dilute hydrochloric acid for 4 hours, washed with deionized water and alcohol for 4 times each, then suction-filtered, and vacuum-dried at 80°C to obtain an amorphous silicon / carbon composite material. figure 1 The curves of temperature and pressure versus time during the preparation of the material. figure 2 It is the XRD diffraction pattern of this material, and the steamed bread peaks around 23° and 27° correspond to amorphous carbon and amorphous silicon in turn. image 3 It is a scanning electron microscope (SEM) photo of the pre...
Embodiment 2
[0033] Under the protective condition of argon atmosphere, magnesium silicide and potassium carbonate with a mass ratio of 0.5:1 were ball-milled at a speed of 400r / min with a ball-to-material ratio of 10:1 for 12 hours, and then the ball-milled uniform mixture was transferred to a closed reaction device; then rise to 100°C at a heating rate of 0.5°C / min for 0.5h and then cool to room temperature;
[0034] The product was sequentially soaked in 1M dilute hydrochloric acid for 4 hours, washed with deionized water and alcohol for 4 times each, then suction-filtered, and vacuum-dried at 70°C to obtain an amorphous silicon / carbon composite material.
[0035] Using the amorphous silicon / carbon composite material obtained in Example 1, an electrode was prepared in the following manner. Amorphous silicon / carbon composite material: super-P: polytetrafluoroethylene was weighed at a mass ratio of 80:10:10, and ground evenly to make an electrode. The metal lithium sheet was used as the c...
Embodiment 3
[0037] Under the protective condition of nitrogen atmosphere, under the protective atmosphere, the mass ratio of magnesium silicide and magnesium carbonate with a mass ratio of 10:1 was ball-milled at a speed of 500r / min with a ball-to-material ratio of 80:1 for 108h, and then the ball-milled uniform mixture was transferred to Airtight reactor; then rise to 500°C at a heating rate of 10°C / min for 5 hours and then cool to room temperature;
[0038] The product was sequentially soaked in 1M dilute hydrochloric acid for 4 hours, washed with deionized water and alcohol for 4 times each, then suction-filtered, and vacuum-dried at 80°C to obtain an amorphous silicon / carbon composite material.
[0039] Using the amorphous silicon / carbon composite material obtained in Example 1, an electrode was prepared in the following manner. Amorphous silicon / carbon composite material: super-P: polytetrafluoroethylene was weighed at a mass ratio of 80:10:10, and ground evenly to make an electrode....
PUM
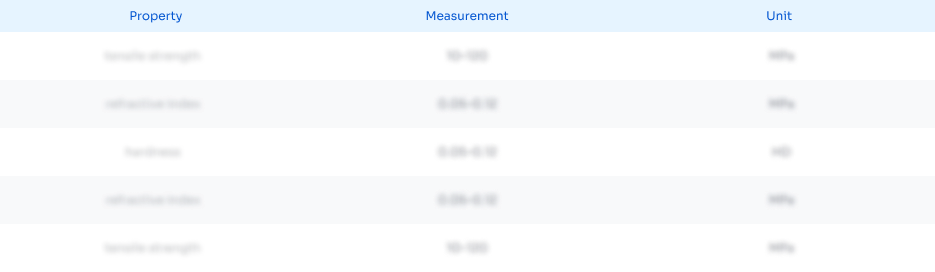
Abstract
Description
Claims
Application Information

- R&D
- Intellectual Property
- Life Sciences
- Materials
- Tech Scout
- Unparalleled Data Quality
- Higher Quality Content
- 60% Fewer Hallucinations
Browse by: Latest US Patents, China's latest patents, Technical Efficacy Thesaurus, Application Domain, Technology Topic, Popular Technical Reports.
© 2025 PatSnap. All rights reserved.Legal|Privacy policy|Modern Slavery Act Transparency Statement|Sitemap|About US| Contact US: help@patsnap.com