A method for preparing dense electrophoretic coating on the surface of magnesium alloy
A technology of electrophoretic coating and magnesium alloy, applied in the direction of coating, electrolytic coating, electrophoretic plating, etc., can solve the problems of easy corrosion of magnesium alloy, uneven surface potential of magnesium alloy, etc., and achieve simple production process and uniform electrophoretic coating , undemanding effects
- Summary
- Abstract
- Description
- Claims
- Application Information
AI Technical Summary
Problems solved by technology
Method used
Image
Examples
Embodiment 1
[0043] (1) Polish the magnesium alloy with 150-mesh, 400-mesh, 800-mesh and 1200-mesh sandpaper, rinse with deionized water, and put it into acetone for 10 minutes of ultrasonication. Weigh 25g of sodium hydroxide, 7.5g of anhydrous sodium carbonate and 1g of sodium dodecylbenzenesulfonate and dissolve them in 500mL of water to make a lye, then put the magnesium alloy into the prepared lye, and place it in a water bath environment at 60°C Alkaline wash in.
[0044] (2) Take AlCl3 and 1-butyl-3-methylimidazole (BMIC) according to the ratio of molar ratio 2:1 and mix and prepare solution, take magnesium alloy as cathode, and the aluminum flake that purity is 99.99% is anode, cathode The distance from the anode is 1 cm. Constant current electrodeposition is adopted, the current density is 10mA / cm2, and the deposition time is 30 minutes for electroplating aluminum.
[0045] (3) Stir the FY-0216 electrophoresis raw material continuously at room temperature for 48 hours to complet...
Embodiment 2
[0048](1) Polish the magnesium alloy with 150-mesh, 400-mesh, 800-mesh and 1200-mesh sandpaper, rinse with deionized water, and put it into acetone for 10 minutes of ultrasonication. Weigh 25g of sodium hydroxide, 7.5g of anhydrous sodium carbonate and 1g of sodium dodecylbenzenesulfonate and dissolve them in 500mL of water to make a lye, then put the magnesium alloy into the prepared lye, and place it in a water bath environment at 60°C Alkaline wash in.
[0049] (2) Take AlCl3 and 1-butyl-3-methylimidazole (BMIC) according to the ratio of molar ratio 2:1 and mix and prepare solution, take magnesium alloy as cathode, and the aluminum flake that purity is 99.99% is anode, cathode The distance from the anode is 2 cm. The constant current electrodeposition is adopted, the current density is 15mA / cm2, and the deposition time is 30 minutes for electroplating aluminum.
[0050] (3) Stir the FY-0216 electrophoresis raw material continuously at room temperature for 48 hours to comp...
Embodiment 3
[0053] (1) Polish the magnesium alloy with 150-mesh, 400-mesh, 800-mesh and 1200-mesh sandpaper, rinse with deionized water, and put it into acetone for 10 minutes of ultrasonication. Weigh 25g of sodium hydroxide, 7.5g of anhydrous sodium carbonate and 1g of sodium dodecylbenzenesulfonate and dissolve them in 500mL of water to make a lye, then put the magnesium alloy into the prepared lye, and place it in a water bath environment at 60°C Alkaline wash in.
[0054] (2) Take AlCl3 and 1-butyl-3-methylimidazole (BMIC) according to the ratio of molar ratio 2:1 and mix and prepare solution, take magnesium alloy as cathode, and the aluminum flake that purity is 99.99% is anode, cathode The distance from the anode is 1 cm. The constant current electrodeposition is adopted, the current density is 10mA / cm2, and the deposition time is 35 minutes for electroplating aluminum.
[0055] (3) Stir the FY-0216 electrophoresis raw material continuously at room temperature for 48 hours to com...
PUM
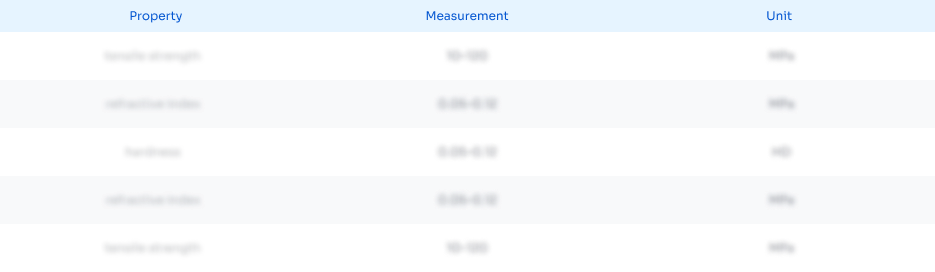
Abstract
Description
Claims
Application Information

- Generate Ideas
- Intellectual Property
- Life Sciences
- Materials
- Tech Scout
- Unparalleled Data Quality
- Higher Quality Content
- 60% Fewer Hallucinations
Browse by: Latest US Patents, China's latest patents, Technical Efficacy Thesaurus, Application Domain, Technology Topic, Popular Technical Reports.
© 2025 PatSnap. All rights reserved.Legal|Privacy policy|Modern Slavery Act Transparency Statement|Sitemap|About US| Contact US: help@patsnap.com