Amphiphilic terpolymer modified ultra-filtration membrane preparation method
A terpolymer and amphiphilic technology, which is applied in the field of membrane separation, can solve the problems of complex chemical graft modification process, decreased hydrophilicity of separation membrane, and unsuitability for industrial production, etc., and achieve high protein retention rate and Anti-pollution ability, avoiding the problem of phase separation, and strong practicability
- Summary
- Abstract
- Description
- Claims
- Application Information
AI Technical Summary
Problems solved by technology
Method used
Image
Examples
Embodiment 1
[0031] This embodiment includes the preparation of polyaryletherketone ultrafiltration membrane;
[0032] 1.5 g of polyarylether ketone was added to the solution containing 8.5 g of NMP, and stirred at 60° C. for 24 hours; then, it was left standing at a constant temperature of 60° C. for 24 hours to obtain a casting solution. Pour the prepared film casting liquid on a clean glass plate and scrape the film; stagnate the liquid film obtained after scraping in the air for 30s, put it into an ultrapure water coagulation bath at 16°C to solidify to form a film; finally The ultrafiltration membrane detached from the glass plate was soaked in ultrapure water for 24 hours to eliminate the residual NMP solvent in the membrane to obtain a polyaryletherketone ultrafiltration membrane.
Embodiment 2
[0034] This embodiment combines the preparation of the amphiphilic terpolymer and the preparation of the amphiphilic terpolymer modified ultrafiltration membrane, including the following steps:
[0035] Step 1, the preparation of amphiphilic terpolymer: first, under nitrogen protection, 1.5g dimethylaminoethyl methacrylate (DMAEMA), 2.2g methacryloyl ethyl sulfobetaine (SBMA), Dissolve 1.4g of vinylpyrrolidone (VP) and 0.5g of AIBN in 100ml of THF-ethanol mixture A with a volume ratio of 5:1, stir and react for 24 hours to obtain a mixed system, pour the mixed system into deionized water, and precipitate Finally, the precipitate was vacuum-dried at 200°C for 12 hours to obtain an amphiphilic terpolymer;
[0036] Step 2, preparation of amphiphilic terpolymer modified ultrafiltration membrane: blend 1.2g of amphiphilic terpolymer with 17mL of NMP to obtain mixed solution B, wherein the concentration of amphiphilic terpolymer 0.6%, sonicate until the amphiphilic terpolymer is co...
Embodiment 3
[0038] This embodiment includes the preparation of amphiphilic terpolymer and the preparation of amphiphilic terpolymer modified ultrafiltration membrane, including the following steps:
[0039] Step 1, the preparation of amphiphilic terpolymer: first, under nitrogen protection, 1.8g dimethylaminoethyl methacrylate (DMAEMA), 2.0g methacryloyl ethyl sulfobetaine (SBMA), 1.7g of vinylpyrrolidone (VP) and 0.35g of AIBN were dissolved in 80ml of tetrahydrofuran and ethanol mixture A with a volume ratio of 5:1, stirred and reacted for 20 hours to obtain a mixed system, and the mixed system was poured into deionized water to precipitate a precipitate ; Finally, vacuum-dry the precipitate at 250°C for 24 hours to obtain an amphiphilic terpolymer;
[0040] Step 2, preparation of amphiphilic terpolymer modified ultrafiltration membrane: 2.0 g of amphiphilic terpolymer is blended with 17 mL of NMP to obtain mixed solution B, wherein the concentration of amphiphilic terpolymer is 1%, so...
PUM
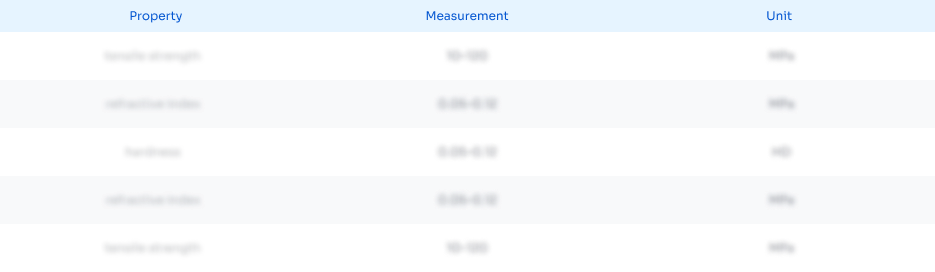
Abstract
Description
Claims
Application Information

- R&D
- Intellectual Property
- Life Sciences
- Materials
- Tech Scout
- Unparalleled Data Quality
- Higher Quality Content
- 60% Fewer Hallucinations
Browse by: Latest US Patents, China's latest patents, Technical Efficacy Thesaurus, Application Domain, Technology Topic, Popular Technical Reports.
© 2025 PatSnap. All rights reserved.Legal|Privacy policy|Modern Slavery Act Transparency Statement|Sitemap|About US| Contact US: help@patsnap.com