A 1050m 3 Preparation process of stuffy charge for high-grade blast furnace
A stuffy furnace and blast furnace technology, which is applied in the field of 1050m3 blast furnace stuffy charge preparation technology, can solve problems such as blast furnace start-up failure, stuffy charge burnout, slag composition unreasonable, etc., and achieve good slag fluidity, hearth The effect of abundant heat and scientific composition of slag
- Summary
- Abstract
- Description
- Claims
- Application Information
AI Technical Summary
Problems solved by technology
Method used
Image
Examples
Embodiment
[0033] A 1050m 3 Preparation method of blast furnace stuffing charge. Specifically, the technical solution includes the following:
[0034] In the step B, the ratio of sintered ore accounts for 85%, the ratio of pelletized ore accounts for 10%, and the ratio of raw ore accounts for 5%.
[0035] In the step B, the ingredients of various raw materials in the furnace charge are as follows.
[0036]
[0037] In the step B, the charging amount of each section is as follows.
[0038]
[0039]
[0040] In the step B, the stuffy charge products are shown in the table below.
[0041]
[0042] Through the preparation of a reasonable and scientific blast furnace material structure, the blast furnace can be shut down for 22 days with a full material line of 1.3 meters. During the start-up process of the blast furnace, the heat in the hearth is abundant, and the slag has good fluidity. After 30 hours of full-air smelting, the utilization factor of the blast furnace reaches ...
PUM
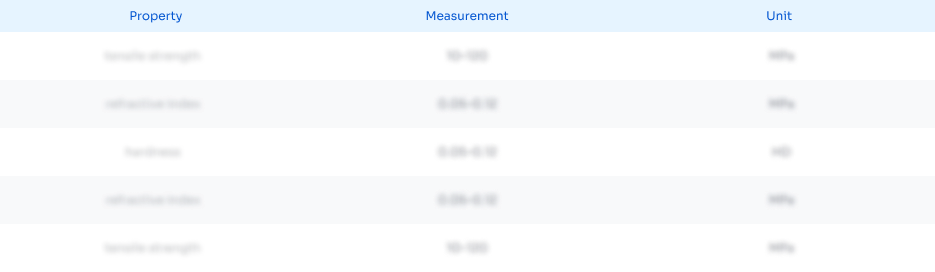
Abstract
Description
Claims
Application Information

- R&D
- Intellectual Property
- Life Sciences
- Materials
- Tech Scout
- Unparalleled Data Quality
- Higher Quality Content
- 60% Fewer Hallucinations
Browse by: Latest US Patents, China's latest patents, Technical Efficacy Thesaurus, Application Domain, Technology Topic, Popular Technical Reports.
© 2025 PatSnap. All rights reserved.Legal|Privacy policy|Modern Slavery Act Transparency Statement|Sitemap|About US| Contact US: help@patsnap.com