Gypsum board drying machine and application thereof
A dryer and gypsum board technology, applied in the direction of progressive dryers, dryers, drying solid materials, etc., can solve the problem that water vapor has not been reasonably recovered and fully utilized, the production line production speed is low, and the appearance quality of products is affected To improve the hydration effect, reduce pitting, and improve the appearance quality of the product
- Summary
- Abstract
- Description
- Claims
- Application Information
AI Technical Summary
Problems solved by technology
Method used
Image
Examples
Embodiment 1
[0053] The length of the inlet preheating section 1 of the dryer is 6 meters (the length of the inlet preheating section of the existing dryer is generally 4 meters), and the time for wet plate preheating is improved by increasing the length of the inlet preheating section 1; A hot air pipeline 5 about 60 meters long is added to introduce the hot air obtained after heat exchange between the hot and humid gas discharged from the second zone 3 of the dryer and the external air into the inlet preheating section 1, thereby increasing the temperature of the inlet preheating section 1, the inlet The amount of hot air in the preheating section 1, thereby increasing the temperature of the wet board when it enters the first zone 2 of the dryer; by mixing the hot water obtained from the waste heat recovery device into the gypsum board molding water, and controlling the amount of dry material used to prepare the gypsum board temperature, thereby increasing the temperature of a control slu...
PUM
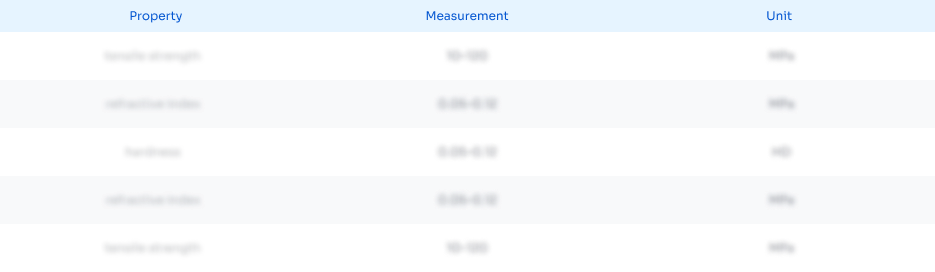
Abstract
Description
Claims
Application Information

- Generate Ideas
- Intellectual Property
- Life Sciences
- Materials
- Tech Scout
- Unparalleled Data Quality
- Higher Quality Content
- 60% Fewer Hallucinations
Browse by: Latest US Patents, China's latest patents, Technical Efficacy Thesaurus, Application Domain, Technology Topic, Popular Technical Reports.
© 2025 PatSnap. All rights reserved.Legal|Privacy policy|Modern Slavery Act Transparency Statement|Sitemap|About US| Contact US: help@patsnap.com