Preparation method and application of high-thermal-conductivity material composite filler
A technology of composite fillers and inorganic thermally conductive fillers, which is applied in the field of thermally conductive materials, can solve the problems that the thermally conductive network is easily damaged, affects the thermally conductive effect, does not have high hardness, etc., and achieves strong bonding, improved wear resistance, and improved thermal conductivity. Effect
- Summary
- Abstract
- Description
- Claims
- Application Information
AI Technical Summary
Problems solved by technology
Method used
Image
Examples
Embodiment 1
[0023] A high thermal conductivity material composite filler, characterized in that it specifically includes the following ingredients in parts by weight: polyamide resin, graphite, inorganic thermal conductivity filler, wear-resistant ceramic powder, carbon fiber, diamond powder, glass fiber, scaly high thermal conductivity carbon powder, Compatibilizer, curing agent, antioxidant;
[0024] Specifically in this embodiment, the following components are included in parts by weight: 42.5 parts of polyamide resin, 40 parts of graphite, 13 parts of inorganic thermally conductive filler, 12.5 parts of wear-resistant ceramic powder, 6.5 parts of carbon fiber, 6.5 parts of diamond powder, 5.5 parts of glass fiber 5.5 parts of flaky high thermal conductivity carbon powder, 3 parts of compatibilizer, 0.35 parts of curing agent, and 0.35 parts of antioxidant.
[0025] Further, the inorganic thermally conductive filler is one or a combination of aluminum oxide, boron nitride, and aluminum...
Embodiment 2
[0033] A high thermal conductivity material composite filler, characterized in that it specifically includes the following ingredients in parts by weight: polyamide resin, graphite, inorganic thermal conductivity filler, wear-resistant ceramic powder, carbon fiber, diamond powder, glass fiber, scaly high thermal conductivity carbon powder, Compatibilizer, curing agent, antioxidant;
[0034] Specifically in the present embodiment, the following components by weight are included: 35 parts of polyamide resin, 30 parts of graphite, 10 parts of inorganic heat-conducting filler, 10 parts of wear-resistant ceramic powder, 3 parts of carbon fiber, 10 parts of diamond powder, 3 parts of glass fiber 1 part, 3 parts of flaky high thermal conductivity carbon powder, 1 part of compatibilizer, 0.2 part of curing agent, 0.2 part of antioxidant.
[0035] Further, the inorganic thermally conductive filler is one or a combination of aluminum oxide, boron nitride, and aluminum nitride.
[0036]...
Embodiment 3
[0043] A high thermal conductivity material composite filler, characterized in that it specifically includes the following ingredients in parts by weight: polyamide resin, graphite, inorganic thermal conductivity filler, wear-resistant ceramic powder, carbon fiber, diamond powder, glass fiber, scaly high thermal conductivity carbon powder, Compatibilizer, curing agent, antioxidant;
[0044] And be specific in the present embodiment, comprise following composition by weight: 60 parts of polyamide resins, 50 parts of graphite, 16 parts of inorganic heat-conducting fillers, 15 parts of wear-resistant ceramic powders, 10 parts of carbon fibers, 10 parts of diamond powders, 8 parts of glass fibers 8 parts, 8 parts of flaky high thermal conductivity carbon powder, 5 parts of compatibilizer, 0.5 part of curing agent, 0.5 part of antioxidant.
[0045] Further, the inorganic thermally conductive filler is one or a combination of aluminum oxide, boron nitride, and aluminum nitride.
[...
PUM
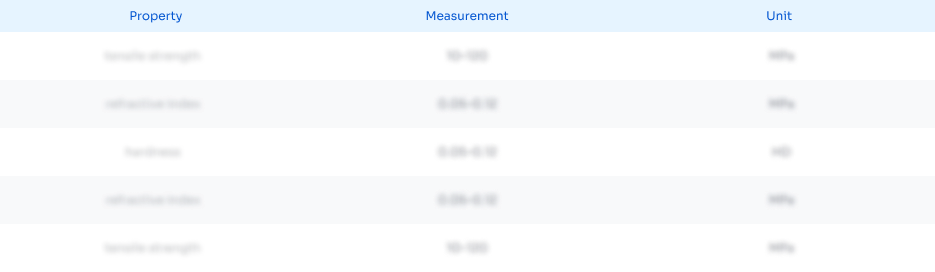
Abstract
Description
Claims
Application Information

- R&D Engineer
- R&D Manager
- IP Professional
- Industry Leading Data Capabilities
- Powerful AI technology
- Patent DNA Extraction
Browse by: Latest US Patents, China's latest patents, Technical Efficacy Thesaurus, Application Domain, Technology Topic, Popular Technical Reports.
© 2024 PatSnap. All rights reserved.Legal|Privacy policy|Modern Slavery Act Transparency Statement|Sitemap|About US| Contact US: help@patsnap.com