Metal magnesium carbon thermal reduction process and device
A metal magnesium and carbothermal technology, applied in the metallurgical industry, can solve the problems of high temperature resistant materials, high energy consumption in the heating process, and high heating costs, and can solve the problems of difficult sealing, lower activation energy, and high electrothermal conversion rate. Effect
- Summary
- Abstract
- Description
- Claims
- Application Information
AI Technical Summary
Problems solved by technology
Method used
Image
Examples
Embodiment 1
[0040] Calcined white with a magnesium oxide content of 36wt%, coke, and fluorite are mixed according to a mass ratio of 60:13:10, ball milled through a 100-mesh sieve, and pressure-formed into a cylindrical sample with a diameter of 6mm and a length of 12mm, and placed in a vacuum reduction furnace Vacuumize between the inner and lower electrodes. Under the pressure of vacuum degree of 1000Pa, the applied current of the sample is controlled at 0.8 ampere, and the energized reaction is cooled after 30 minutes. The reduction rate of magnesium oxide in the measured sample is 61%.
Embodiment 2
[0042] Calcined white with a magnesium oxide content of 36wt%, coke, and fluorite are mixed according to a mass ratio of 60:30:10, ball milled through a 100-mesh sieve, and pressure-formed into a cylindrical sample with a diameter of 6mm and a length of 12mm, and placed in a vacuum reduction furnace Vacuumize between the inner and lower electrodes. Under the pressure of vacuum degree of 100Pa, the applied current of the sample is controlled at 0.8 ampere, and the energization reaction is cooled after 23 minutes. The reduction rate of magnesium oxide in the sample is measured to be 65%.
Embodiment 3
[0044]Calcined white with a magnesium oxide content of 36wt%, coke, and fluorite were mixed according to a mass ratio of 60:35:10, ball milled through a 200-mesh sieve, and formed into a cylindrical sample with a diameter of 6mm and a length of 12mm under a pressure of 25Mpa, and placed in Vacuum is drawn between the upper and lower electrodes in the vacuum reduction furnace. Under the pressure of vacuum degree of 2000Pa, the applied current of the sample is controlled at 0.8 ampere, and the energized reaction is cooled after 10 minutes. The reduction rate of magnesium oxide in the sample is measured to be 67%.
PUM
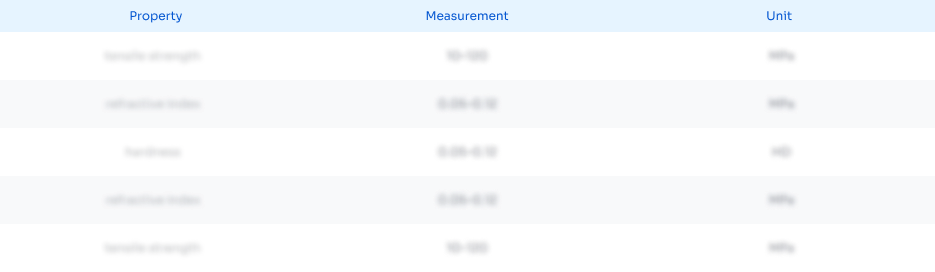
Abstract
Description
Claims
Application Information

- R&D
- Intellectual Property
- Life Sciences
- Materials
- Tech Scout
- Unparalleled Data Quality
- Higher Quality Content
- 60% Fewer Hallucinations
Browse by: Latest US Patents, China's latest patents, Technical Efficacy Thesaurus, Application Domain, Technology Topic, Popular Technical Reports.
© 2025 PatSnap. All rights reserved.Legal|Privacy policy|Modern Slavery Act Transparency Statement|Sitemap|About US| Contact US: help@patsnap.com