Temperature-controlled cooling process and device of forge pieces
A technology for temperature-controlled cooling and forging, applied in the processing field of forgings, can solve the problems of reduced mechanical properties of forgings, increased resource consumption, and high production costs, and achieves uniform metallographic and grain size, low maintenance costs, and high mechanical properties. Effect
- Summary
- Abstract
- Description
- Claims
- Application Information
AI Technical Summary
Problems solved by technology
Method used
Image
Examples
Embodiment 1
[0022] A temperature-controlled cooling process for forgings. The steps of the temperature-controlled cooling process are: (1) taking out the forging after final forging and placing it on a mesh belt; The cooling rate of cooling is 9 degrees per second, and the cooling time of cooling is 40 seconds; (3) the forgings processed in step (2) are turned over, and the second cooling process is carried out. The cooling rate of cooling is 3 degrees per second, and the cooling The cooling time is 22 seconds; (4) the forging after the temperature control cooling treatment in step (3) is taken out from the mesh belt, placed in the air and naturally cooled to normal temperature to obtain the finished forging.
Embodiment 2
[0024] A temperature-controlled cooling process for forgings. The steps of the temperature-controlled cooling process are: (1) taking out the forging after final forging and placing it on a mesh belt; The cooling rate of cooling is 11 degrees per second, and the cooling time of cooling is 44 seconds; (3) the forgings processed in step (2) are turned over, and the second cooling process is carried out. The cooling rate of cooling is 4 degrees per second, and the cooling The cooling time is 24 seconds; (4) the forging after the temperature control cooling treatment in step (3) is taken out from the mesh belt, placed in the air and naturally cooled to normal temperature to obtain the finished forging.
Embodiment 3
[0026] A temperature-controlled cooling process for forgings. The steps of the temperature-controlled cooling process are: (1) taking out the forging after final forging and placing it on a mesh belt; The cooling rate of cooling is 12 degrees per second, and the cooling time of cooling is 50 seconds; (3) the forgings processed in step (2) are turned over, and the second cooling process is carried out, and the cooling rate of cooling is 5 degrees per second. The cooling time is 26 seconds; (4) the forging after the temperature-controlled cooling treatment in step (3) is taken out from the mesh belt, placed in the air and naturally cooled to normal temperature to obtain the finished forging.
PUM
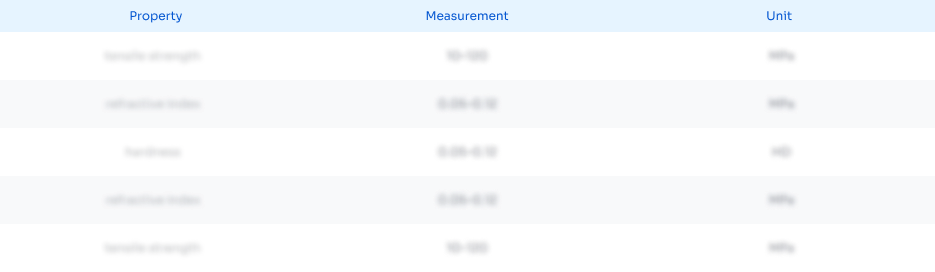
Abstract
Description
Claims
Application Information

- R&D Engineer
- R&D Manager
- IP Professional
- Industry Leading Data Capabilities
- Powerful AI technology
- Patent DNA Extraction
Browse by: Latest US Patents, China's latest patents, Technical Efficacy Thesaurus, Application Domain, Technology Topic, Popular Technical Reports.
© 2024 PatSnap. All rights reserved.Legal|Privacy policy|Modern Slavery Act Transparency Statement|Sitemap|About US| Contact US: help@patsnap.com