A two-stage down-entrained entrained bed ironmaking system and ironmaking process
An entrained flow bed, two-stage technology, applied in the field of two-stage descending entrained entrained bed ironmaking process, can solve the problems of low reduction efficiency, unrealized process simplicity, low energy consumption, low waste heat recovery rate, etc., to achieve improved reduction efficiency, Effects of reduced footprint and reduced complexity
- Summary
- Abstract
- Description
- Claims
- Application Information
AI Technical Summary
Problems solved by technology
Method used
Image
Examples
Embodiment 1
[0052] like figure 1 As shown, a two-stage downdraft bed ironmaking process device (arrangement 1) has a structure including a melting furnace section 4, which is an airflow descending bed, a basic combustion / gasifier 1 is set on the top, and the upper side is The first inlet 2 for coke (coal) powder (air, water vapor), the pre-reduction mineral powder inlet-the second inlet 3 is set at a distance below it; the mineral powder pre-reduction furnace section 8 is an air flow descending bed, and the upper side is a pre- Hot mineral powder inlet-the fourth inlet 7, the lower part is connected to the inlet of the pre-reduced mineral powder separator-the first separator 9; the melting furnace section 4 and the mineral powder pre-reduction furnace section 8 are connected through the slag pool 5; cooling, temperature adjustment and tempering The medium inlet-the third inlet 6 is set at the connecting pipe between the slag pool 5 and the mineral powder pre-reduction furnace section 8; t...
Embodiment 2
[0063] like figure 2 Shown is another embodiment of the present application. A two-stage descending entrained entrained bed ironmaking process device (arrangement mode 2) has a structure including a melting furnace section 4, which is an airflow descending bed, a basic combustion / gasifier 1 is arranged on the top, and coke powder ( Air, water vapor) inlet-the first inlet 2, a pre-reduced mineral powder inlet-the second inlet 3 is set at a distance below it; the mineral powder pre-reduction furnace section 8 is an airflow descending bed, and the upper side is the mineral powder inlet-the fourth Inlet 7, the lower part is connected to the pre-reduction mineral powder separator-the first separator 9 inlet; the melting furnace section 4 and the mineral powder pre-reduction furnace section 8 are connected through the slag pool 5; the cooling, temperature-regulating and tempering medium inlet-the third inlet 6 is set At the connecting pipe between the slag pool 5 and the mineral p...
PUM
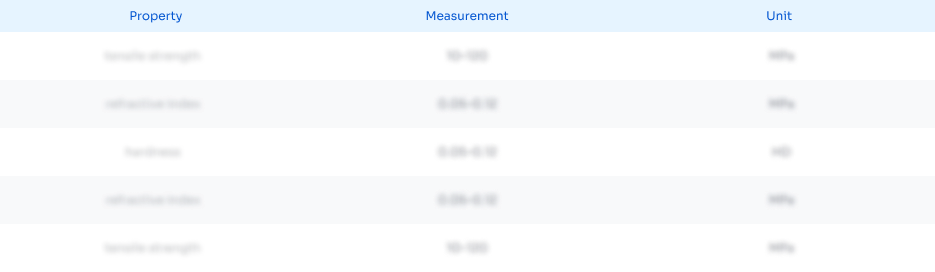
Abstract
Description
Claims
Application Information

- R&D
- Intellectual Property
- Life Sciences
- Materials
- Tech Scout
- Unparalleled Data Quality
- Higher Quality Content
- 60% Fewer Hallucinations
Browse by: Latest US Patents, China's latest patents, Technical Efficacy Thesaurus, Application Domain, Technology Topic, Popular Technical Reports.
© 2025 PatSnap. All rights reserved.Legal|Privacy policy|Modern Slavery Act Transparency Statement|Sitemap|About US| Contact US: help@patsnap.com