Composite sound insulation plate and production process thereof
A board and preparation process technology, which is applied in the field of composite sound-insulating boards and its production technology, can solve the problems of low strength, poor thermal insulation effect, poor sound insulation effect, etc., and achieve the effect of simple preparation process, good sound insulation effect, easy to obtain raw materials and environmental protection
- Summary
- Abstract
- Description
- Claims
- Application Information
AI Technical Summary
Problems solved by technology
Method used
Examples
Embodiment 1
[0025] A composite sound insulation board, which includes the following raw materials in parts by weight: 35 parts of bentonite, 6 parts of wood fiber, 5 parts of perlite particles, 4 parts of activated carbon, 6 parts of plant straw powder, 2 parts of light burnt magnesium oxide, yellow 3 parts of raw rubber powder, 5 parts of expanded vermiculite, 5 parts of silica fume, 10 parts of polyacrylamide, 5 parts of binder.
[0026] A preparation process of a composite sound insulation board includes the following steps: Step 1. Weigh bentonite, wood fiber, perlite particles, activated carbon, plant straw powder, light burnt magnesium oxide, xanthan gum powder, expanded vermiculite, Silica fume, polyacrylamide and binder, ready for use; step two, mix bentonite with 3 times its weight of water to obtain a bentonite mixture; step three, mix wood fiber, perlite particles, activated carbon and light burnt magnesium oxide Stir to obtain a mixture; the stirring speed is 200r / min; step four,...
Embodiment 2
[0028] A composite sound-insulating board, comprising the following raw materials in parts by weight: 40 parts of bentonite, 15 parts of wood fiber, 10 parts of perlite particles, 8 parts of activated carbon, 11 parts of plant straw powder, 5 parts of light burnt magnesium oxide, yellow 7 parts of raw rubber powder, 10 parts of expanded vermiculite, 7 parts of silica fume, 20 parts of polyacrylamide, 9 parts of binder.
[0029] A preparation process of a composite sound insulation board includes the following steps: Step 1. Weigh bentonite, wood fiber, perlite particles, activated carbon, plant straw powder, light burnt magnesium oxide, xanthan gum powder, expanded vermiculite, Silica fume, polyacrylamide and binder, ready for use; step two, mix bentonite with 5 times its weight of water to obtain a bentonite mixture; step three, mix wood fiber, perlite particles, activated carbon and light-burned magnesium oxide Stir to obtain a mixture; the stirring speed is 300r / min; step four...
Embodiment 3
[0031] A composite sound insulation board, which includes the following raw materials in parts by weight: 38 parts of bentonite, 10 parts of wood fiber, 7 parts of perlite particles, 6 parts of activated carbon, 9 parts of plant straw powder, 4 parts of light burnt magnesium oxide, yellow 5 parts of raw rubber powder, 7 parts of expanded vermiculite, 6 parts of silica fume, 15 parts of polyacrylamide, 7 parts of binder.
[0032] A preparation process of a composite sound insulation board includes the following steps: Step 1. Weigh bentonite, wood fiber, perlite particles, activated carbon, plant straw powder, light burnt magnesium oxide, xanthan gum powder, expanded vermiculite, Silica fume, polyacrylamide and binder, ready for use; step two, mix bentonite with 4 times its weight of water to obtain a bentonite mixture; step three, mix wood fiber, perlite particles, activated carbon and light burnt magnesium oxide Stir to obtain a mixture; the stirring speed is 240r / min; step four...
PUM
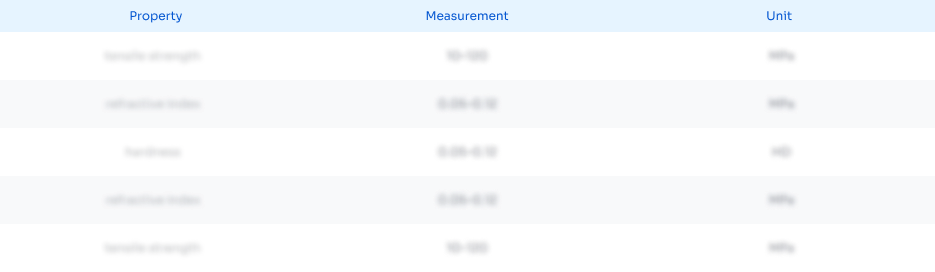
Abstract
Description
Claims
Application Information

- Generate Ideas
- Intellectual Property
- Life Sciences
- Materials
- Tech Scout
- Unparalleled Data Quality
- Higher Quality Content
- 60% Fewer Hallucinations
Browse by: Latest US Patents, China's latest patents, Technical Efficacy Thesaurus, Application Domain, Technology Topic, Popular Technical Reports.
© 2025 PatSnap. All rights reserved.Legal|Privacy policy|Modern Slavery Act Transparency Statement|Sitemap|About US| Contact US: help@patsnap.com