Self-adaption machining system and control method thereof and car body machining equipment
A processing system and self-adaptive technology, applied in the field of mechanical processing, can solve problems such as increased processing costs, harsh working environment, flying dust, etc., and achieve the effects of reduced production and labor costs, safe and environmentally friendly production, and high consistency of precision
- Summary
- Abstract
- Description
- Claims
- Application Information
AI Technical Summary
Problems solved by technology
Method used
Image
Examples
Embodiment Construction
[0030] The specific embodiment of the present invention will be described in further detail by describing the embodiments below with reference to the accompanying drawings, the purpose is to help those skilled in the art to have a more complete, accurate and in-depth understanding of the concept and technical solutions of the present invention, and contribute to its implementation.
[0031] Such as Figure 1 to Figure 3 As shown, the present invention provides an adaptive machining system for the machining of a workpiece 5, more specifically for post-processing of milling the weld seam of a workpiece 5 that has undergone preliminary machining such as MIG welding . The adaptive processing system includes a control device 8, a visual detection device 3 for scanning the workpiece to obtain detection data, a milling tool head 1 for processing the workpiece, an electric spindle 2 for driving the movement of the milling tool head 3, and The electric spindle 2 is connected by trans...
PUM
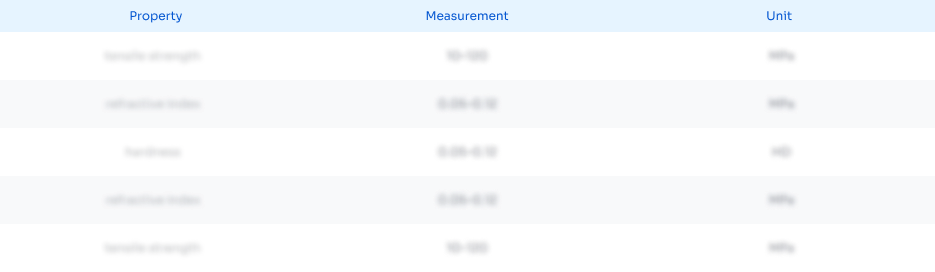
Abstract
Description
Claims
Application Information

- Generate Ideas
- Intellectual Property
- Life Sciences
- Materials
- Tech Scout
- Unparalleled Data Quality
- Higher Quality Content
- 60% Fewer Hallucinations
Browse by: Latest US Patents, China's latest patents, Technical Efficacy Thesaurus, Application Domain, Technology Topic, Popular Technical Reports.
© 2025 PatSnap. All rights reserved.Legal|Privacy policy|Modern Slavery Act Transparency Statement|Sitemap|About US| Contact US: help@patsnap.com