Deep hole pre-splitting and blasting method in primary mining and primary caving process of extra-thick coal seam working face
A technology of pre-splitting blasting and extra-thick coal seam, which is applied in blasting and other directions, and can solve problems such as the lack of methods to improve the coal recovery rate during the initial mining and initial discharge of extra-thick coal seams
- Summary
- Abstract
- Description
- Claims
- Application Information
AI Technical Summary
Problems solved by technology
Method used
Image
Examples
Embodiment Construction
[0022] The deep hole pre-splitting blasting method during the initial mining and initial discharge of the extra-thick coal seam working face is realized by the following steps:
[0023] 1) Carry out the first deep hole pre-splitting blasting on the whole working face before operation, specifically:
[0024] 1) A bolter drill equipped with a φ42 alloy steel drill bit is used for blasthole construction (compared with traditional construction drilling, which is safer, faster and more efficient), and a blasthole is constructed between adjacent supports. Perpendicular to the top plate, the blast holes are arranged at the 200mm outward of the bracket cut-off line (the hinge of the hydraulic support top beam and the cover beam);
[0025] 2) Construct the charge pipe, one end of the φ40mm×4000mm PVC pipe is filled with 300mm loess, and from the other end, 3 rolls of gunpowder, 1 roll of blasting primer, 3 rolls of gunpowder, 1 roll of blasting primer, and 3 rolls are sequentially load...
PUM
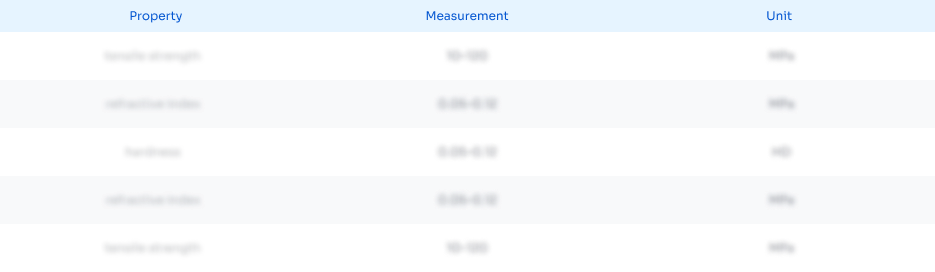
Abstract
Description
Claims
Application Information

- R&D
- Intellectual Property
- Life Sciences
- Materials
- Tech Scout
- Unparalleled Data Quality
- Higher Quality Content
- 60% Fewer Hallucinations
Browse by: Latest US Patents, China's latest patents, Technical Efficacy Thesaurus, Application Domain, Technology Topic, Popular Technical Reports.
© 2025 PatSnap. All rights reserved.Legal|Privacy policy|Modern Slavery Act Transparency Statement|Sitemap|About US| Contact US: help@patsnap.com