Halogen-free flame-retardant cable material
A technology of flame retardant cable materials and raw materials, applied in circuits, electrical components, plastic/resin/wax insulators, etc. The effect of improving elongation at break, reducing resource waste and environmental pollution, and facilitating recycling
- Summary
- Abstract
- Description
- Claims
- Application Information
AI Technical Summary
Problems solved by technology
Method used
Image
Examples
Embodiment 1
[0024] A method for polyvinyl chloride cold-resistant high flame-retardant cable material, comprising the following steps:
[0025] Step 1, weighing each component raw material according to parts by weight;
[0026] Step 2, polyvinyl chloride resin 100Kg, epoxy soybean oil 4Kg, polyethylene wax 0.3Kg, diisononyl phthalate 15Kg, dioctyl terephthalate 20Kg, calcium zinc composite stabilizer 4Kg, plant ash 3Kg , 2Kg of zinc oxide and 0.5Kg of hydroxy silicone oil are added in the internal mixer and carried out banburying, and the masterbatch is obtained;
[0027] Step 3, adding 10Kg of magnesium hydroxide, 15Kg of aluminum hydroxide, 10Kg of magnesium aluminum hydrotalcite and 1Kg of paraffin oil to the internal mixer of step 2, blending and banburying, to obtain rubber compound;
[0028] Step 4, transferring the rubber material to a twin-screw extruder for extrusion and granulation, drying the pellets, and cooling to room temperature to obtain the halogen-free flame-retardant c...
Embodiment 2
[0031] A method for polyvinyl chloride cold-resistant high flame-retardant cable material, comprising the following steps:
[0032] Step 1, weighing each component raw material according to parts by weight;
[0033] Step 2, polyvinyl chloride resin 120Kg, epoxy soybean oil 8Kg, polyethylene wax 0.55Kg, diisononyl phthalate 22.5Kg, dioctyl terephthalate 24Kg, calcium zinc composite stabilizer 7Kg, plant ash 6Kg, 4Kg of zinc oxide and 1.15Kg of hydroxyl silicone oil are added to the internal mixer for internal mixing to obtain the masterbatch;
[0034] Step 3, adding 14Kg of magnesium hydroxide, 24.5Kg of aluminum hydroxide, 14Kg of magnesium aluminum hydrotalcite and 2.5Kg of paraffin oil to the internal mixer of step 2, blending and banburying, to obtain rubber compound;
[0035] Step 4, transferring the rubber material to a twin-screw extruder for extrusion and granulation, drying the pellets, and cooling to room temperature to obtain the halogen-free flame-retardant cable m...
Embodiment 3
[0038] A method for polyvinyl chloride cold-resistant high flame-retardant cable material, comprising the following steps:
[0039] Step 1, weighing each component raw material according to parts by weight;
[0040] Step 2, polyvinyl chloride resin 140Kg, epoxy soybean oil 12Kg, polyethylene wax 0.8Kg, diisononyl phthalate 30Kg, dioctyl terephthalate 28Kg, calcium zinc composite stabilizer 10Kg, plant ash 9Kg , 6Kg of zinc oxide and 1.8Kg of hydroxy silicone oil are added in the internal mixer and carried out banburying, and masterbatch is obtained;
[0041] Step 3, adding 18Kg of magnesium hydroxide, 27Kg of aluminum hydroxide, 18Kg of magnesium aluminum hydrotalcite and 4Kg of paraffin oil in the banbury mixer of step 2, blending and banburying, obtained sizing material;
[0042] Step 4, transferring the rubber material to a twin-screw extruder for extrusion and granulation, drying the pellets, and cooling to room temperature to obtain the halogen-free flame-retardant cable...
PUM
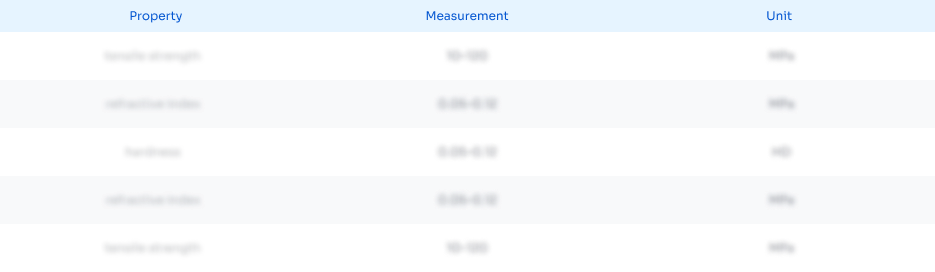
Abstract
Description
Claims
Application Information

- Generate Ideas
- Intellectual Property
- Life Sciences
- Materials
- Tech Scout
- Unparalleled Data Quality
- Higher Quality Content
- 60% Fewer Hallucinations
Browse by: Latest US Patents, China's latest patents, Technical Efficacy Thesaurus, Application Domain, Technology Topic, Popular Technical Reports.
© 2025 PatSnap. All rights reserved.Legal|Privacy policy|Modern Slavery Act Transparency Statement|Sitemap|About US| Contact US: help@patsnap.com