Method for preparing interior trim material for automobile seat cover
A technology for interior materials and car seats, which is used in motor vehicles, road vehicles, vehicle parts, etc., can solve problems such as large human injuries, and achieve the effects of good corrosion resistance, excellent performance, and soft and smooth film formation.
- Summary
- Abstract
- Description
- Claims
- Application Information
AI Technical Summary
Problems solved by technology
Method used
Image
Examples
Embodiment 1
[0030] In parts by weight, weigh 50 parts of chloroprene rubber, 50 parts of ethylene propylene rubber, 3 parts of zinc oxide, 1 part of stearic acid, 1 part of accelerator CBS, 15 parts of dioctyl phthalate, and Butadiene rubber, stearic acid, accelerator CBS and dioctyl phthalate are mixed and placed in the rubber mixer, and the temperature is 20°C, and the thin pass is masticated for 3 times to obtain the mixture A, which is added to the mixture For ethylene-propylene rubber, continue to thin-pass plasticating for 3 times to obtain the mixture B, add zinc oxide to the mixture B, and thin-pass 4 times to get the modified rubber; according to the mass ratio of 1:1:10 Mix rubber, nylon and dichloromethane, stir at room temperature and high speed for 8 hours at a stirring speed of 1000r / min, and then obtain a spinning solution, inject the spinning solution into a syringe for electrospinning, use an aluminum foil as a receiving device, and spin at a voltage of 15kV, the receivin...
Embodiment 2
[0032] In parts by weight, weigh 55 parts of chloroprene rubber, 55 parts of ethylene propylene rubber, 4 parts of zinc oxide, 2 parts of stearic acid, 2 parts of accelerator CBS, 17 parts of dioctyl phthalate, and Butadiene rubber, stearic acid, accelerator CBS and dioctyl phthalate are mixed and placed in a rubber mixer, and the temperature is 30°C and Botong is plasticized for 4 times to obtain the mixture A. Add to the mixture For ethylene-propylene rubber, continue to thin-pass plasticizing for 4 times to obtain the mixture B, add zinc oxide to the mixture B, and thin-pass 4 times to produce the modified rubber; the modified rubber is obtained according to the mass ratio 1:1:10 Mix rubber, nylon and dichloromethane, stir at room temperature and high speed at a stirring speed of 1100r / min for 10h, and then obtain a spinning solution, inject the spinning solution into a syringe for electrospinning, use aluminum foil as a receiving device, and spin at a voltage of 17kV, the ...
Embodiment 3
[0034] In parts by weight, weigh 60 parts of chloroprene rubber, 60 parts of ethylene propylene rubber, 5 parts of zinc oxide, 3 parts of stearic acid, 3 parts of accelerator CBS, 20 parts of dioctyl phthalate, and Butadiene rubber, stearic acid, accelerator CBS and dioctyl phthalate are mixed and placed in a rubber mixer, and the temperature is 40°C, and the thin pass is plasticized for 5 times to obtain the mixture A, and the mixture is added For ethylene-propylene rubber, continue to make plasticizing 5 times with Botong to obtain the mixture B, add zinc oxide to the mixture B, and make the sheet through 5 times to get the modified rubber; Mix rubber, nylon and dichloromethane, and stir at room temperature and high speed for 12 hours at a stirring speed of 1200r / min to obtain a spinning solution, inject the spinning solution into a syringe for electrospinning, and use an aluminum foil as a receiving device, and the spinning voltage is 20kV, the receiving distance is 12cm, a...
PUM
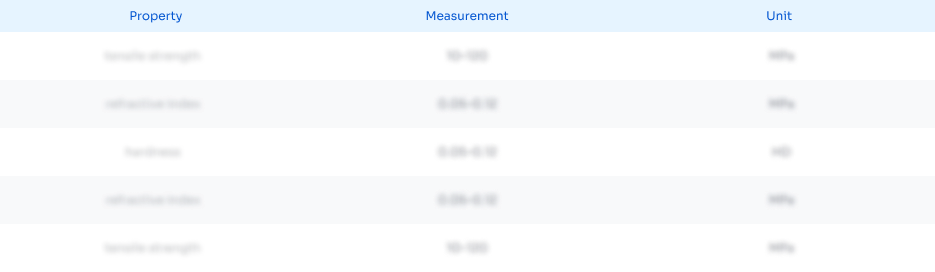
Abstract
Description
Claims
Application Information

- Generate Ideas
- Intellectual Property
- Life Sciences
- Materials
- Tech Scout
- Unparalleled Data Quality
- Higher Quality Content
- 60% Fewer Hallucinations
Browse by: Latest US Patents, China's latest patents, Technical Efficacy Thesaurus, Application Domain, Technology Topic, Popular Technical Reports.
© 2025 PatSnap. All rights reserved.Legal|Privacy policy|Modern Slavery Act Transparency Statement|Sitemap|About US| Contact US: help@patsnap.com