Preparation process of rubber composite material for oil-resistant sealing rubber strip
A sealing strip and composite material technology, applied in the field of sealing strips, can solve the problems of poor sealing effect and corrosion of sealing strips, and achieve the effect of high anti-aging, high anti-corrosion ability and excellent corrosion resistance
- Summary
- Abstract
- Description
- Claims
- Application Information
AI Technical Summary
Problems solved by technology
Method used
Image
Examples
Embodiment 1
[0033] The invention provides a preparation process of a rubber composite material for an oil-resistant sealing strip, wherein the main materials used (by weight) include: 90-110 parts of NBR, 3.5-4.5 parts of an active agent, stearin Acid SA: 0.38-0.42 parts, filler 56-64 parts, sulfur S 0.48-0.52 parts, accelerator 0.7-0.9 parts, cold-resistant plasticizer DOA 5-7 parts, anti-aging agent 4-5 parts , the vulcanizing agent DCP is 2.3-2.7 parts;
[0034] The active agent is specifically zinc oxide (ZnO);
[0035] The accelerator specifically includes: accelerator DM and accelerator CZ, and the mass ratio of accelerator DM and accelerator CZ is: 0.2-0.3:0.5-0.6;
[0036] The filler specifically includes: carbon black N330 and carbon black N550, and the mass ratio of carbon black N330 and carbon black N550 is: 16-24:36-44, which can give the sealing strip a bright black color, not only that, but also has anti-ultraviolet , acid and alkali resistance and other functions;
[003...
Embodiment 2
[0054] Specifically in the present embodiment, the major ingredients (by weight) used therein include: NBR is 110 parts, activator is 4 parts, stearic acid SA is: 0.4 part, carbon black N330 is 20 parts, and Carbon black N550 is 40 parts, sulfur S is 0.5 parts, accelerator DM is 0.25 parts, accelerator CZ is 0.55 parts, cold-resistant plasticizer DOA is 6 parts, antioxidant RD is 1 part, antioxidant 4010NA is 1.1 parts, The anti-aging agent AW is 1.4 parts, the anti-aging agent NBC is 1 part, the paraffin is 1 part, and the vulcanizing agent DCP is 2.5 parts:
[0055] A preparation process of a rubber composite material for an oil-resistant sealing strip, the specific preparation steps are as follows:
[0056] S1, mixing;
[0057] S1.1. First clean the two rollers of the two-roll mill, and then adjust the distance between the two rollers to 1mm, and carry out plasticizing of raw rubber NBR. When raw rubber NBR is plasticized, a two-roll mill is used for thin pass 2 Second, t...
Embodiment 3
[0070] Specifically in the present embodiment, the major ingredients used (by weight) include: NBR is 110 parts, activator is 3.5 parts, stearic acid SA is: 0.42 parts, carbon black N330 is 16 parts, and Carbon black N550 is 44 parts, sulfur S is 0.48 parts, accelerator DM is 0.3 parts, accelerator CZ is 0.5 parts, cold-resistant plasticizer DOA is 7 parts, anti-aging agent RD is 0.8 parts, anti-aging agent 4010NA is 1.2 parts, The anti-aging agent AW is 1.2 parts, the anti-aging agent NBC is 1.2 parts, the paraffin is 0.8 parts, and the vulcanizing agent DCP is 2.7 parts:
[0071] A preparation process of a rubber composite material for an oil-resistant sealing strip, the specific preparation steps are as follows:
[0072] S1, mixing;
[0073] S1.1. First clean the two rollers of the two-roll mill, and then adjust the distance between the two rollers to 1mm, and carry out plasticizing of raw rubber NBR. When raw rubber NBR is plasticized, a two-roll mill is used for thin pas...
PUM
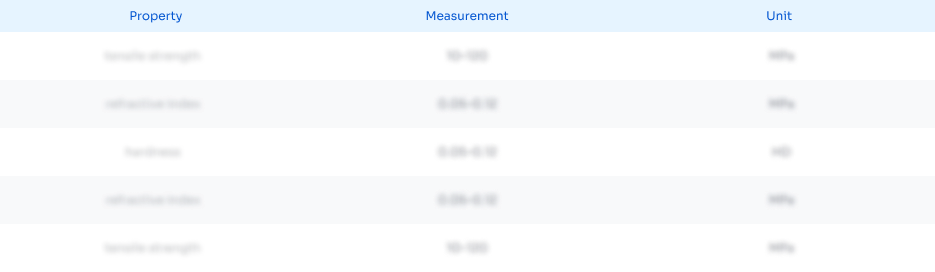
Abstract
Description
Claims
Application Information

- R&D
- Intellectual Property
- Life Sciences
- Materials
- Tech Scout
- Unparalleled Data Quality
- Higher Quality Content
- 60% Fewer Hallucinations
Browse by: Latest US Patents, China's latest patents, Technical Efficacy Thesaurus, Application Domain, Technology Topic, Popular Technical Reports.
© 2025 PatSnap. All rights reserved.Legal|Privacy policy|Modern Slavery Act Transparency Statement|Sitemap|About US| Contact US: help@patsnap.com