Rigid polyurethane foam plastic and preparation method thereof
A technology of rigid foam plastics and polyurethane, applied in the field of foam plastics, can solve the problems of low closed cell ratio, influence on product strength, low compressive strength, etc., and achieve stable chemical properties, easy manual operation, and small thermal conductivity Effect
- Summary
- Abstract
- Description
- Claims
- Application Information
AI Technical Summary
Problems solved by technology
Method used
Image
Examples
Embodiment 1
[0039] A preparation method for rigid polyurethane foam, comprising the steps of:
[0040] a with 40 parts of vegetable oil polyether polyols; 20 parts of petroleum polyester polyols; 10 parts of polyethylene oxide polyols; 1 part of pentamethyldialkylene triamine; 4 parts of esters, 6 parts of trialkyl phosphates); After mixing, a mixture is obtained;
[0041] b. Control the temperature of the mixture at 30-40°C. Under the condition of ambient temperature of 30-35°C, quickly add 3 parts of silicone oil as a stabilizer; 20 parts of water as a foaming agent; 0.02 parts of stannous octoate as an organometallic catalyst ; Under the condition of controlling the rotational speed of 1000-2000r / min, stirring for 10-20s to obtain the combined material;
[0042] c. Pour the obtained combination into a polyurethane foaming mold, quickly cover and lock the mold, and release the mold in 15 to 20 minutes to obtain rigid polyurethane foam.
[0043] Polyurethane foam mold includes:
[004...
Embodiment 2
[0061] A preparation method for rigid polyurethane foam, comprising the steps of:
[0062] a with 42 parts of vegetable oil polyether polyols; 22 parts of petroleum polyester polyols; 13 parts of polyethylene oxide polyols; 1.4 parts of pentamethyldialkylene triamines; 14 parts of flame retardants (trialkyl 5 parts of phosphoric acid esters, 9 parts of tetraalkyl diphosphonate compounds); After mixing, a mixture is obtained;
[0063] b. Control the temperature of the mixture at 30-40°C. Under the condition of ambient temperature of 30-35°C, quickly add 3.5 parts of silicone oil as a stabilizer; 22 parts of water as a foaming agent; 0.02 parts of stannous octoate as an organometallic catalyst ; Under the condition of controlling the rotational speed of 1000-2000r / min, stirring for 10-20s to obtain the combined material;
[0064] c. Pour the obtained combination into a polyurethane foaming mold, quickly cover and lock the mold, and release the mold in 15 to 20 minutes to obtain...
Embodiment 3
[0069] A preparation method for rigid polyurethane foam, comprising the steps of:
[0070] a with 46 parts of vegetable oil polyether polyols; 24 parts of petroleum polyester polyols; 16 parts of polyethylene oxide polyols; 1.6 parts of pentamethyldialkylene triamines; 8 parts of esters, 4 parts of trialkyl phosphates, 8 parts of tetraalkyl diphosphonate compounds); after mixing, a mixture is obtained;
[0071] b. Control the temperature of the mixture at 30-40°C. Under the condition of ambient temperature of 30-35°C, quickly add 3.6 parts of silicone oil as a stabilizer; 24 parts of water as a foaming agent; 0.03 parts of stannous octoate as an organometallic catalyst ;Under the condition of controlling the rotational speed of 1000-2000r / min, stirring for 10-20s to obtain the combined material;
[0072] c. Pour the obtained combination into a polyurethane foaming mold, quickly cover and lock the mold, and release the mold in 15 to 20 minutes to obtain rigid polyurethane foam...
PUM
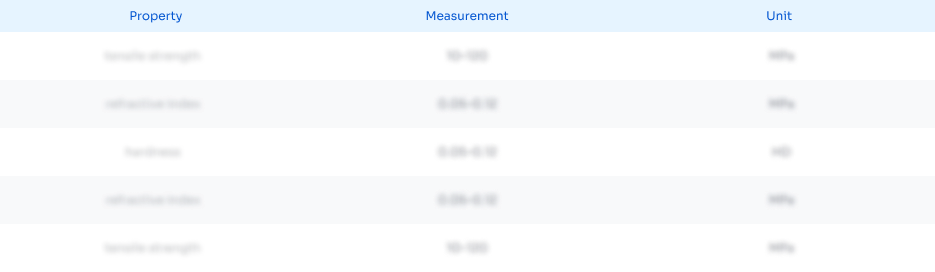
Abstract
Description
Claims
Application Information

- R&D
- Intellectual Property
- Life Sciences
- Materials
- Tech Scout
- Unparalleled Data Quality
- Higher Quality Content
- 60% Fewer Hallucinations
Browse by: Latest US Patents, China's latest patents, Technical Efficacy Thesaurus, Application Domain, Technology Topic, Popular Technical Reports.
© 2025 PatSnap. All rights reserved.Legal|Privacy policy|Modern Slavery Act Transparency Statement|Sitemap|About US| Contact US: help@patsnap.com