Production method of pressure-resistant impact-resistant thermal insulation building material
A technology for impact resistance and building materials, applied in sustainable waste treatment, solid waste management, climate sustainability, etc., can solve the problems of impact, poor mechanical strength, and easy damage of thermal insulation building materials, and achieve mechanical strength and thermal insulation performance. Strengthen, improve thermal insulation performance, improve the effect of structural strength
- Summary
- Abstract
- Description
- Claims
- Application Information
AI Technical Summary
Problems solved by technology
Method used
Image
Examples
example 1
[0037] Preparation of thermal reaction products:
[0038] Put the concentrated organic product and distilled water into a beaker at a mass ratio of 1:10, place the beaker in a shaker, and oscillate for 2 hours at a frequency of 32-36kHz. After shaking, add 10% mass fraction to the beaker. Adjust the pH value of sodium hydroxide solution to 9, and continue to shake for 4 hours to prepare an alkaline reaction solution;
[0039] Put the above alkaline reaction solution into a suction filter for suction filtration to obtain filter residue, wash the filter residue with distilled water 3 times, put the filter residue into a high-temperature furnace, raise the temperature in the furnace to 110°C, and preheat the furnace for 40 minutes at a constant temperature to fill the furnace With argon, the temperature in the furnace was raised to 600℃ again, and the reaction was carried out at a constant temperature for 2 hours. After the reaction, the hot reaction product was obtained by grinding; ...
example 2
[0046] Preparation of thermal reaction products:
[0047] Put the concentrated organic product and distilled water into a beaker at a mass ratio of 1:10, place the beaker in a shaker, and shake for 2h at a frequency of 34kHz. After shaking, add 11% mass fraction of hydrogen to the beaker. Adjust the pH value of the sodium solution to 9, and continue shaking for 4 hours to prepare an alkaline reaction solution;
[0048] Put the above alkaline reaction liquid into a suction filter for suction filtration to obtain filter residue, wash the filter residue with distilled water 3 to 5 times, put the filter residue into a high-temperature furnace, raise the temperature in the furnace to 115°C, and preheat the furnace for 45 minutes. Fill it with argon gas, raise the temperature in the furnace to 620°C again, react for 2 hours at a constant temperature, and grind after the reaction to obtain a hot reaction product;
[0049] Preparation of concentrated organic products:
[0050] Put cotton and...
example 3
[0056] Preparation of thermal reaction products:
[0057] Put the concentrated organic product and distilled water into a beaker at a mass ratio of 1:10, place the beaker in a shaker, and shake for 3 hours at a frequency of 36kHz. After shaking, add 12% mass fraction of hydrogen to the beaker. Adjust the pH value of the sodium solution to 10, continue to shake for 5 hours to prepare an alkaline reaction solution;
[0058] Put the above alkaline reaction liquid into a suction filter for suction filtration to obtain the filter residue, wash the filter residue with distilled water 5 times, put the filter residue into a high-temperature furnace, raise the temperature in the furnace to 120°C, preheat at a constant temperature for 50 minutes, and fill the furnace With argon, the temperature in the furnace was raised to 650℃ again, and the reaction was carried out at a constant temperature for 3 hours. After the reaction, the hot reaction product was obtained by grinding; the preparation ...
PUM
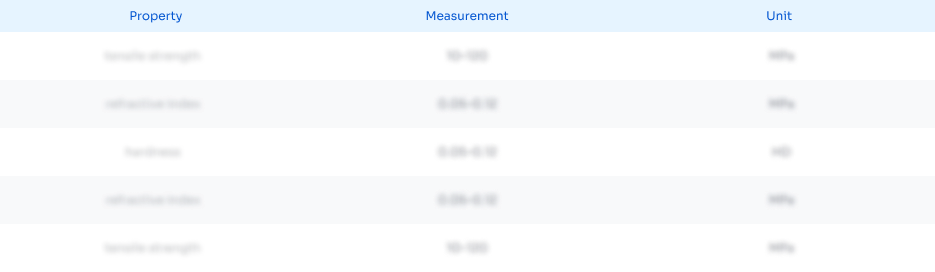
Abstract
Description
Claims
Application Information

- R&D
- Intellectual Property
- Life Sciences
- Materials
- Tech Scout
- Unparalleled Data Quality
- Higher Quality Content
- 60% Fewer Hallucinations
Browse by: Latest US Patents, China's latest patents, Technical Efficacy Thesaurus, Application Domain, Technology Topic, Popular Technical Reports.
© 2025 PatSnap. All rights reserved.Legal|Privacy policy|Modern Slavery Act Transparency Statement|Sitemap|About US| Contact US: help@patsnap.com