Aluminum-niobium-tantalum intermediate alloy and preparing method thereof
A technology of master alloy and niobium tantalum, applied in the field of aluminum niobium tantalum master alloy and its preparation, can solve the problems of titanium alloy quality influence, refractory metal, poor alloy uniformity, etc., to improve uniform stability, meet production requirements, and improve The effect of production requirements
- Summary
- Abstract
- Description
- Claims
- Application Information
AI Technical Summary
Problems solved by technology
Method used
Image
Examples
preparation example Construction
[0023] The present invention provides a method for preparing an aluminum-niobium-tantalum master alloy described in the above scheme, comprising the following steps:
[0024] (1) Mix tantalum pentoxide, niobium pentoxide and aluminum for aluminothermic reaction, and obtain an aluminum-niobium-tantalum primary alloy after cooling;
[0025] (2) Vacuum smelting the aluminum-niobium-tantalum primary alloy and aluminum, and obtaining an aluminum-niobium-tantalum master alloy after cooling.
[0026] In the invention, tantalum pentoxide, niobium pentoxide and aluminum are mixed for aluminothermic reaction, and the primary alloy of aluminum, niobium and tantalum is obtained after cooling. In the present invention, an exothermic agent is preferably added to the mixture of the tantalum pentoxide, niobium pentoxide and aluminum; the exothermic agent is preferably potassium chlorate. In the present invention, the mass ratio of the tantalum pentoxide, niobium pentoxide and aluminum is pre...
Embodiment 1
[0034] 1. Aluminum thermal smelting process
[0035] (1) Dry the aluminum powder, niobium pentoxide, tantalum pentoxide, and potassium chlorate at a drying temperature of 120° C. for 12 hours.
[0036] (2) Raw material ratio: 68.06kg of aluminum powder, 15.65kg of niobium pentoxide, 42.74kg of tantalum pentoxide, and 25.00kg of potassium chlorate. Put the raw materials into a V-shaped mixer and mix them well to ensure the contact between raw materials full.
[0037] (3) Put the uniformly mixed charge into the sintered corundum crucible, ignite and react, and after cooling for 6 hours, remove the crucible, take out the alloy ingot, and weigh it.
[0038] (4) After removing the slag layer and oxide film on the surface of the alloy ingot, crush and finish it to 5-50 mm, and obtain the primary alloy of aluminum, niobium and tantalum after magnetic separation and manual selection.
[0039] 2. Vacuum melting process
[0040] (1) The aluminum powder and the primary alloy of alumin...
Embodiment 2
[0047] 1. Aluminum thermal smelting process
[0048] (1) Dry the aluminum powder, niobium pentoxide, tantalum pentoxide, and potassium chlorate at a drying temperature of 120° C. for 12 hours.
[0049] (2) Raw material ratio: 68.88kg of aluminum powder, 13.37kg of niobium pentoxide, and 42.74kg of tantalum pentoxide. Put the raw materials into a V-shaped mixer and mix them well to ensure sufficient contact between raw materials.
[0050] (3) Put the uniformly mixed charge into the sintered corundum crucible, ignite and react, and after cooling for 6 hours, remove the crucible, take out the alloy ingot, and weigh it.
[0051] (4) After removing the slag layer and oxide film on the surface of the alloy ingot, crush and finish it to 5-50 mm, and obtain the primary alloy of aluminum, niobium and tantalum after magnetic separation and manual selection.
[0052] 2. Vacuum melting process
[0053] (1) Dry the aluminum powder and the primary alloy at a temperature of 120° C. and a d...
PUM
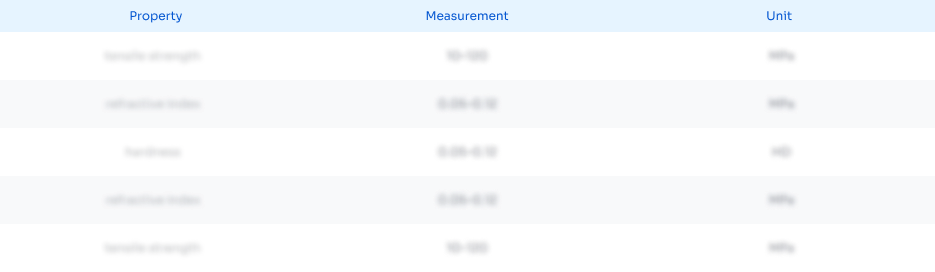
Abstract
Description
Claims
Application Information

- R&D
- Intellectual Property
- Life Sciences
- Materials
- Tech Scout
- Unparalleled Data Quality
- Higher Quality Content
- 60% Fewer Hallucinations
Browse by: Latest US Patents, China's latest patents, Technical Efficacy Thesaurus, Application Domain, Technology Topic, Popular Technical Reports.
© 2025 PatSnap. All rights reserved.Legal|Privacy policy|Modern Slavery Act Transparency Statement|Sitemap|About US| Contact US: help@patsnap.com