Magnesium alloy cutting fluid resistant to bimetallic contact corrosion and preparation method thereof
A technology of contact corrosion and magnesium alloys, applied in lubricating compositions, petroleum industry, additives, etc., can solve the problems of bimetallic contact corrosion and lack of bimetallic contact corrosion performance, and achieve good stability in hard water and excellent salt load resistance Effect
- Summary
- Abstract
- Description
- Claims
- Application Information
AI Technical Summary
Problems solved by technology
Method used
Image
Examples
Embodiment example 1
[0035] The main raw materials are expressed in parts by weight as:
[0036]
[0037]
[0038] Among them, the composite antirust agent is the reaction product of component A, component B and component C.
[0039] Component A: 36.7 parts of a mixture of methyldiethanolamine and triethanolamine
[0040] Component B: 8.0 parts of dodecanedibasic acid
[0041] Component C: 55.3 parts of mixture of tall oil acid and alcohol ether carboxylic acid
[0042] The preparation process is as follows: put component A and component B into the reaction kettle in sequence according to the above ratio, heat to 60±5°C and stir, after the solid material is completely reacted to a clear and transparent state, add component C, and continue stirring for 30 minutes until the reaction completely.
[0043] Wherein, component A: the weight ratio of methyldiethanolamine and triethanolamine is 6:1
[0044] Component C: The weight ratio of tall oil acid and alcohol ether carboxylic acid is 1:1.5 ...
Embodiment example 2
[0058] The main raw materials are expressed in parts by weight as:
[0059]
[0060] Among them, the composite antirust agent is the reaction product of component A, component B and component C.
[0061] Component A: 38 parts of mixture of methyldiethanolamine and triethanolamine
[0062] Component B: 10 parts of dodecanedibasic acid
[0063] Component C: 52 parts of mixture of tall oil acid and alcohol ether carboxylic acid
[0064] The preparation process is: put component A and component B into the reaction kettle in sequence according to the above ratio, heat to 60±5°C and stir, after the solid material is completely reacted to a clear and transparent state, add component C, and continue stirring for 30 minutes until the reaction completely.
[0065] Wherein, component A: the weight ratio of methyldiethanolamine and triethanolamine is 6:1
[0066] Component C: The weight ratio of tall oil acid and alcohol ether carboxylic acid is 1:1.5
[0067] Composite phosphorus-c...
Embodiment example 3
[0080] The main raw materials are expressed in parts by weight as:
[0081]
[0082]
[0083] Among them, the composite antirust agent is the reaction product of component A, component B and component C.
[0084] Component A: 23 parts of mixture of methyldiethanolamine and triethanolamine
[0085] Component B: 12 parts of dodecanedioic acid
[0086] Component C: 65 parts of a mixture of tall oil acid and alcohol ether carboxylic acid;
[0087] The preparation process is: put component A and component B into the reaction kettle in sequence according to the above ratio, heat to 60±5°C and stir, after the solid material is completely reacted to a clear and transparent state, add component C, and continue stirring for 30 minutes until the reaction completely.
[0088] Wherein, component A: the weight ratio of methyldiethanolamine and triethanolamine is 4:1
[0089] Component C: The weight ratio of tall oil acid and alcohol ether carboxylic acid is 1:1.5
[0090] Compo...
PUM
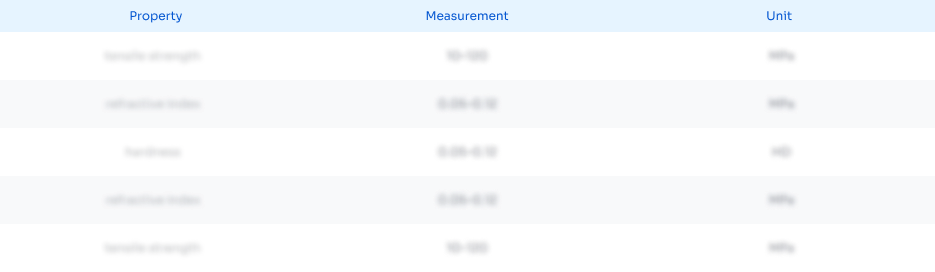
Abstract
Description
Claims
Application Information

- R&D
- Intellectual Property
- Life Sciences
- Materials
- Tech Scout
- Unparalleled Data Quality
- Higher Quality Content
- 60% Fewer Hallucinations
Browse by: Latest US Patents, China's latest patents, Technical Efficacy Thesaurus, Application Domain, Technology Topic, Popular Technical Reports.
© 2025 PatSnap. All rights reserved.Legal|Privacy policy|Modern Slavery Act Transparency Statement|Sitemap|About US| Contact US: help@patsnap.com