Preparation method of slow-drying waterborne acrylic resin
A water-based acrylic acid and acrylic acid technology, applied in the field of polymer materials, can solve the problems affecting the application of water-based acrylic resin, and achieve the effect of good moisture retention, convenient operation, and not easy to block the network
- Summary
- Abstract
- Description
- Claims
- Application Information
AI Technical Summary
Problems solved by technology
Method used
Examples
Embodiment 1
[0023] (1) add 5 parts of anionic emulsifier A-102, 3 parts of sodium bisulfate and 100 parts of deionized water in the reactor, heat up to 40 ° C, stir until the anionic emulsifier A-102 and sodium bisulfate are completely dissolved and mixed ;
[0024] (2) Add 0.2 parts of ammonium persulfate, 8 parts of styrene, 4 parts of acrylonitrile, 6 parts of n-butyl acrylate, 4 parts of ethyl acrylate in another reaction kettle, and then add 1 part of diacetone acrylamide after mixing evenly Pre-emulsification is carried out, and the pre-emulsion is obtained after being completely dissolved and mixed uniformly;
[0025] (3) Weigh 5% of the pre-emulsion and add it to the reaction kettle, add the pre-emulsion dropwise when the temperature is raised to 80°C, and react at a constant temperature for 4 hours;
[0026] (4) After stopping the reaction, keep the temperature for 1 hour, naturally cool down to 60° C. for post-processing, remove the residual monomer, adjust the pH, and filter t...
Embodiment 2
[0028] (1) add 7.5 parts of anionic emulsifier A-102, 4.5 parts of sodium bisulfate and 125 parts of deionized water in the reaction kettle, heat up to 45 ° C, stir until the anionic emulsifier A-102 and sodium bisulfate are completely dissolved and mixed ;
[0029] (2) In another reaction kettle, add 1.1 parts of sodium persulfate, 14 parts of n-butyl acrylate, 6 parts of ethyl acrylate, 12 parts of styrene, 8 parts of methyl methacrylate, and then add 1 part of dimethacrylate after mixing evenly Acetone acrylamide is pre-emulsified, and the pre-emulsion is obtained after being completely dissolved and mixed uniformly;
[0030] (3) Weigh 7.5% of the pre-emulsion and add it to the reaction kettle, add the pre-emulsion dropwise when the temperature is raised to 81°C, and react at a constant temperature for 4 hours;
[0031] (4) After stopping the reaction, keep the temperature for 1 hour, naturally cool down to 60° C. for post-processing, remove the residual monomer, adjust th...
Embodiment 3
[0033] (1) add 10 parts of anionic emulsifier A-102, 6 parts of sodium bisulfate and 150 parts of deionized water in the reaction kettle, heat up to 50 ° C, stir until the anionic emulsifier A-102 and sodium bisulfate are completely dissolved and mixed ;
[0034] (2) Add 0.2 parts of azobisisobutyronitrile, 18 parts of n-butyl acrylate, 12 parts of ethyl acrylate, 16 parts of styrene, 14 parts of methyl methacrylate in another reaction kettle, and then add after mixing evenly 5 parts of diacetone acrylamide are pre-emulsified, and the pre-emulsion is obtained after being completely dissolved and mixed uniformly;
[0035] (3) Weigh 10% of the pre-emulsion and add it to the reaction kettle, add the pre-emulsion dropwise when the temperature is raised to 82°C, and react at a constant temperature for 4 hours;
[0036] (4) After stopping the reaction, keep the temperature for 1 hour, naturally cool down to 60° C. for post-processing, remove the residual monomer, adjust the pH, and...
PUM
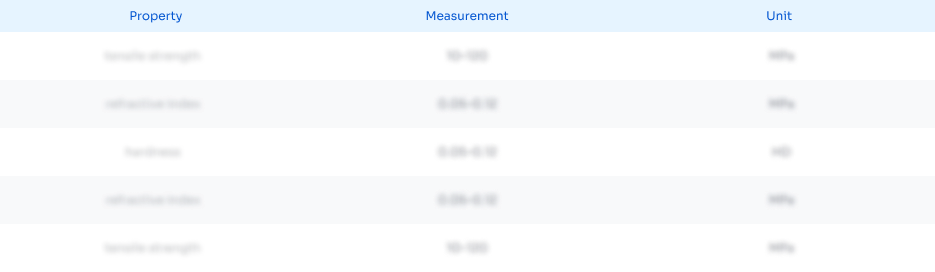
Abstract
Description
Claims
Application Information

- Generate Ideas
- Intellectual Property
- Life Sciences
- Materials
- Tech Scout
- Unparalleled Data Quality
- Higher Quality Content
- 60% Fewer Hallucinations
Browse by: Latest US Patents, China's latest patents, Technical Efficacy Thesaurus, Application Domain, Technology Topic, Popular Technical Reports.
© 2025 PatSnap. All rights reserved.Legal|Privacy policy|Modern Slavery Act Transparency Statement|Sitemap|About US| Contact US: help@patsnap.com