Current loading method used during pulse current auxiliary precision blanking machining
A pulse current and precision blanking technology, which is applied in metal processing, metal processing equipment, manufacturing tools, etc., can solve the problem of insufficient blanking capacity of high-strength steel plates
- Summary
- Abstract
- Description
- Claims
- Application Information
AI Technical Summary
Problems solved by technology
Method used
Image
Examples
Embodiment Construction
[0029] The present invention has electric heating effect and electroplasticity when the current acts on the metal, and the electric eddy current effect of the high-frequency pulse current acting on the cavity and the micro-crack has the ability to heal the plastic strain damage of the metal. In view of the fact that the pulse current assisted plastic forming process can significantly reduce the strength of metal materials and comprehensively improve its formability and machinability, the present invention introduces electroplasticity, pulse current repair and healing of internal cavities and microcracks in metal materials, and electrothermal softening effects. In the fine blanking technology, the difficulty of fine blanking of high-strength steel plates is reduced; the electrothermal effect is also used to cause the metal material in the area near the punching edge to heat up and expand, so as to alleviate the excessive drop of hydrostatic stress in the shear area of the metal...
PUM
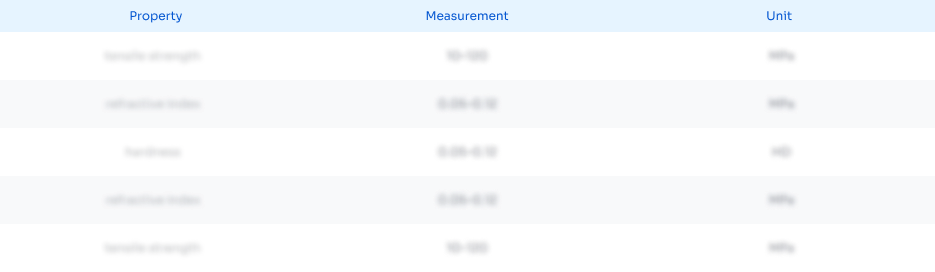
Abstract
Description
Claims
Application Information

- R&D
- Intellectual Property
- Life Sciences
- Materials
- Tech Scout
- Unparalleled Data Quality
- Higher Quality Content
- 60% Fewer Hallucinations
Browse by: Latest US Patents, China's latest patents, Technical Efficacy Thesaurus, Application Domain, Technology Topic, Popular Technical Reports.
© 2025 PatSnap. All rights reserved.Legal|Privacy policy|Modern Slavery Act Transparency Statement|Sitemap|About US| Contact US: help@patsnap.com