Corrosion resistance and high temperature resistance magnesium alloy wheel hub and preparation method thereof
A magnesium alloy, high-temperature-resistant technology, applied in wheel manufacturing, wheels, web-type wheels, etc., can solve the problems of easy damage and beauty, and achieve the effect of improving appearance, strengthening surface strength and avoiding wear
- Summary
- Abstract
- Description
- Claims
- Application Information
AI Technical Summary
Problems solved by technology
Method used
Examples
Embodiment 1
[0049] A corrosion-resistant and high-temperature magnesium alloy wheel hub, wherein the mass percentage of the magnesium alloy includes the following alloy elements: Al: 4.0-6.5%, Zn: 1.2-3.0%, Mn: 0.8-1.5%, Yb: 0.1-3.3%, N : 0.3 to 0.8%, Si: 0.8 to 2.3%, Cr: 18 to 25%, W: ≤2.5%, Zr: 0.2 to 0.6%, and the balance is Mg and inevitable impurity elements. The outer surface of the wheel hub is processed by micro-arc oxidation to form a ceramic film on the surface of the product, which is then baked and sprayed with paint.
[0050] A ceramic film is formed on the surface of the product of the invention, which strengthens the surface strength, and prevents the protective layer from breaking due to abrasion, bumping and scratching of the wheel. At the same time, the overall performance and appearance of the magnesium alloy core are improved by adding trace elements that are resistant to high temperature and oxidation.
[0051] Preferably, the mass percentage of the magnesium alloy i...
Embodiment 2
[0059] A method for manufacturing a corrosion-resistant and high-temperature magnesium alloy wheel hub, comprising the following steps:
[0060] Step 1. Preheating: use a composite crucible, the inner layer is made of heat-resistant boiler steel with a thickness of 20mm to 30mm, and the outer layer is made of stainless steel plates with a thickness of 4mm to 6mm by explosion and composite, and the magnesium ingot is preheated at 100 ℃. Heat for 60min, then heat up to 300℃ for 60min;
[0061] Step 2. Alloying: the magnesium ingot is melted, and heated to 680℃~700℃ to add trace elements; mechanically stir for 15min, and pour SF into the closed environment of the magnesium alloy liquid 6 and CO 2 Mix gas, let stand for 90min, and heat to 725℃~740℃ for 60min;
[0062] Step 3, refining: 750℃~760℃, using PFD anaerobic refining;
[0063] Step 4. Casting: cooling to 695℃~705℃, using medium frequency electromagnetic casting;
[0064] Step 5, material preparation: homogenize the cas...
PUM
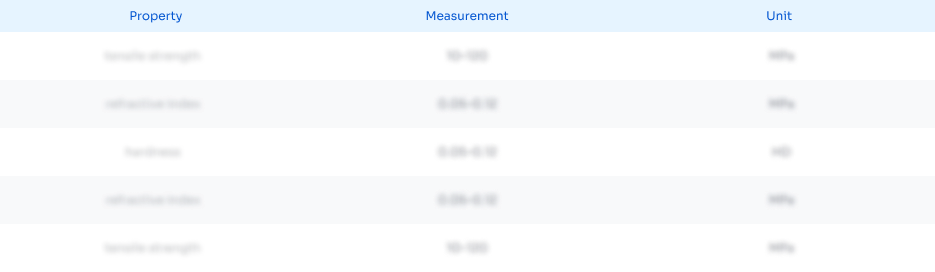
Abstract
Description
Claims
Application Information

- Generate Ideas
- Intellectual Property
- Life Sciences
- Materials
- Tech Scout
- Unparalleled Data Quality
- Higher Quality Content
- 60% Fewer Hallucinations
Browse by: Latest US Patents, China's latest patents, Technical Efficacy Thesaurus, Application Domain, Technology Topic, Popular Technical Reports.
© 2025 PatSnap. All rights reserved.Legal|Privacy policy|Modern Slavery Act Transparency Statement|Sitemap|About US| Contact US: help@patsnap.com