Methods for preparing quicklime from calcium carbide dry residue and producing nano calcium carbonate by adopting quicklime
A nano-calcium carbonate and quicklime technology is applied in the field of calcium carbide slag resource utilization and development to achieve high value-added utilization and solve the problems of land occupation and environmental pollution.
- Summary
- Abstract
- Description
- Claims
- Application Information
AI Technical Summary
Problems solved by technology
Method used
Examples
Embodiment 1
[0015] Embodiment 1: the moisture content is 1.5%, and the calcium carbide dry slag that main component is calcium carbonate is ground into powder, washes with clear water, suction filtration, is placed in oven at 110 o C drying. Then put it in the muffle furnace, at 950 o Calcined at C for 2 hours to obtain quicklime with a calcium oxide content of 86.13%. Take 5.0g of the obtained quicklime, add 70ml of water, and dissolve 7.15g of NH 4 Cl was slowly added to the calcium carbide slag solution, at 40 o C, reacted for 60min under the condition of 400r / min, filtered and removed the precipitate to obtain calcium chloride solution, then added 2ml triethanolamine and 50ml0.5mol / L sodium carbonate solution to it, at 20 o C, under the condition of 400r / min, reacted for 30min, suction filtered, after washing with distilled water and absolute ethanol respectively, then the resulting precipitate was placed in an oven, 110 o C drying for 2 hours to obtain calcite-type nano-calcium c...
Embodiment 2
[0016] Embodiment 2: the moisture content is 2.1%, and the calcium carbide dry slag that main component is calcium carbonate is ground into powder, washes with clear water, suction filtration, is placed in oven at 110 o C drying. Then put it in the muffle furnace, at 1000 o Calcined at C for 3 hours to obtain quicklime with a calcium oxide content of 87.24%. Take 5.0g of the obtained quicklime, add 100ml of water, and dissolve 8.24g of NH 4 Cl was slowly added to the calcium carbide slag solution, at 20 o C, under the condition of 300r / min, react for 60min, filter and remove the precipitate, obtain calcium chloride solution, then add 3ml triethanolamine and 50ml0.5mol / L sodium carbonate solution to it, at 40 o C, reacted for 60min under the condition of 400r / min, suction filtered, after washing with distilled water and absolute ethanol respectively, then the resulting precipitate was placed in an oven, 110 o C drying for 2 hours to obtain calcite-type nano-calcium carbonat...
Embodiment 3
[0017] Embodiment 3: the moisture content is 4.7%, and the calcium carbide dry slag of main component is ground into powder, washes with clear water, suction filtration, is placed in oven at 110 o C drying. Then put it in the muffle furnace, at 1100 o Calcined at C for 3 hours to obtain quicklime with a calcium oxide content of 88.68%. Take 5.0g of the obtained quicklime, add 50ml of water, and dissolve 9.02g of NH 4 Cl was slowly added to the calcium carbide slag solution, at 50 o C, reacted for 60min under the condition of 400r / min, filtered to remove the precipitate, obtained calcium chloride solution, then added 5ml triethanolamine and 25ml1.0mol / L sodium carbonate solution to it, at 60 o C, under the condition of 400r / min, reacted for 30min, suction filtered, after washing with distilled water and absolute ethanol respectively, then the resulting precipitate was placed in an oven, 110 o C drying for 2 hours to obtain calcite-type nano-calcium carbonate with a purity o...
PUM
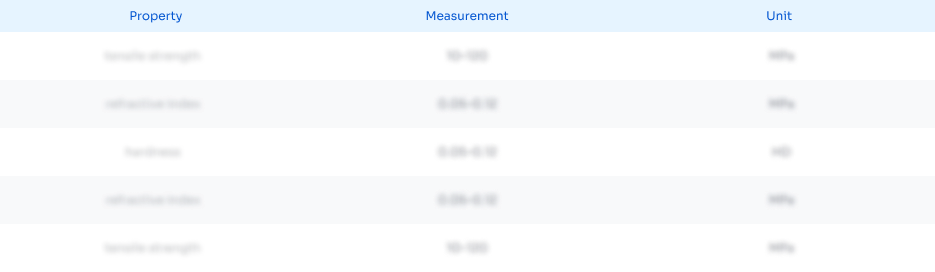
Abstract
Description
Claims
Application Information

- R&D
- Intellectual Property
- Life Sciences
- Materials
- Tech Scout
- Unparalleled Data Quality
- Higher Quality Content
- 60% Fewer Hallucinations
Browse by: Latest US Patents, China's latest patents, Technical Efficacy Thesaurus, Application Domain, Technology Topic, Popular Technical Reports.
© 2025 PatSnap. All rights reserved.Legal|Privacy policy|Modern Slavery Act Transparency Statement|Sitemap|About US| Contact US: help@patsnap.com