High-efficiency treatment method for heavy metal solid waste and treatment furnace
A treatment method and technology of treatment furnace, which are applied in the direction of furnace, furnace type, and process efficiency improvement, etc., can solve the problems of deterioration of furnace condition, increase of processing material volume, high diaphragm layer, etc.
- Summary
- Abstract
- Description
- Claims
- Application Information
AI Technical Summary
Problems solved by technology
Method used
Image
Examples
Embodiment Construction
[0039] Such as Figure 1 to Figure 7 As shown, in the high-efficiency treatment method for heavy metal solid waste disclosed in this embodiment, the treatment furnace adopted is a rectangular vertical structure, the furnace hearth is made of refractory materials, and the part of the furnace wall corresponding to the slag layer is a copper water jacket. The furnace is divided into three different functional areas: smelting area, reduction area and clarification separation area.
[0040] There are smelting primary tuyeres 4 and smelting secondary tuyeres 3 on both sides of the furnace wall in the smelting area. The height of the smelting primary tuyeres is located in the molten slag layer. The smelting primary tuyeres are equipped with submerged jet burners RSQ. The patent number is ZL201821168025.2 , the top is provided with a feeding port 1, a smelting recombustion chamber 2 and a smelting waste heat boiler 6. An oxygen injection pipe is installed in the smelting secondary tu...
PUM
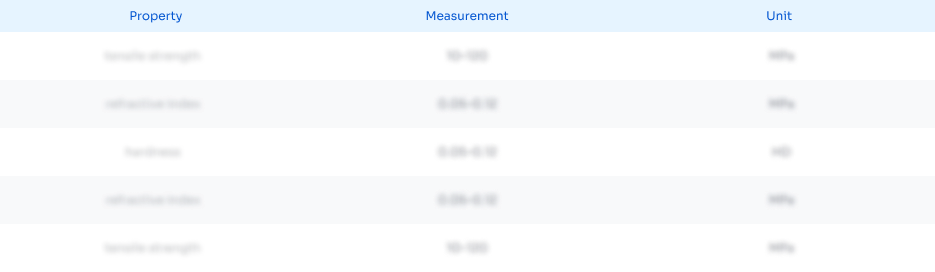
Abstract
Description
Claims
Application Information

- R&D Engineer
- R&D Manager
- IP Professional
- Industry Leading Data Capabilities
- Powerful AI technology
- Patent DNA Extraction
Browse by: Latest US Patents, China's latest patents, Technical Efficacy Thesaurus, Application Domain, Technology Topic, Popular Technical Reports.
© 2024 PatSnap. All rights reserved.Legal|Privacy policy|Modern Slavery Act Transparency Statement|Sitemap|About US| Contact US: help@patsnap.com