System and method for grinding part weld joint based on vision guide robot
A vision-guided and robotic technology, which is applied to the parts of grinding machine tools, the control of workpiece feed movement, and the machine tools suitable for grinding the edge of workpieces, etc., can solve the problems that are not conducive to the health of workers, the quality of products cannot be guaranteed, and the efficiency of enterprises. high-quality production
- Summary
- Abstract
- Description
- Claims
- Application Information
AI Technical Summary
Problems solved by technology
Method used
Image
Examples
Embodiment Construction
[0045] In order to make the purpose, technical solution and advantages of the present invention clearer, the technical solution of the present invention will be described in detail below. Apparently, the described embodiments are only some of the embodiments of the present invention, but not all of them. Based on the embodiments of the present invention, all other implementations obtained by persons of ordinary skill in the art without making creative efforts fall within the protection scope of the present invention.
[0046] figure 1 It is a structural schematic diagram provided by an embodiment of the vision-guided robot grinding component weld seam system of the present invention.
[0047] like figure 1 and figure 2 As shown, the vision-guided robot-based system for grinding component welds described in this embodiment includes:
[0048] Laser sensor 1, image acquisition module 2, host computer 3, robot 4 and floating grinding head 5;
[0049] Wherein, the laser senso...
PUM
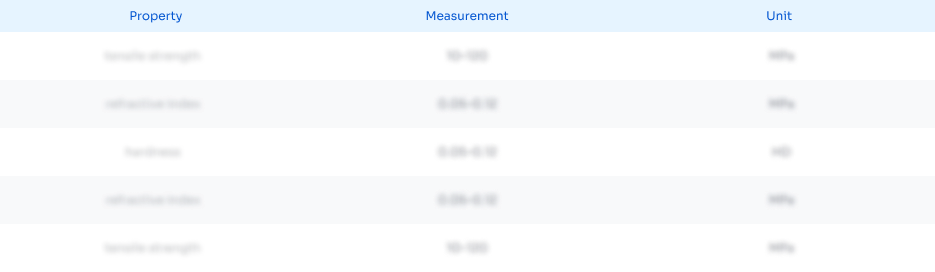
Abstract
Description
Claims
Application Information

- R&D
- Intellectual Property
- Life Sciences
- Materials
- Tech Scout
- Unparalleled Data Quality
- Higher Quality Content
- 60% Fewer Hallucinations
Browse by: Latest US Patents, China's latest patents, Technical Efficacy Thesaurus, Application Domain, Technology Topic, Popular Technical Reports.
© 2025 PatSnap. All rights reserved.Legal|Privacy policy|Modern Slavery Act Transparency Statement|Sitemap|About US| Contact US: help@patsnap.com