Double-headed spinning system and double-headed spinning method
A clamping and head technology, applied in the field of pipe processing equipment, can solve problems such as low production efficiency and complicated pipe material transfer system, and achieve the effects of improving efficiency, simplifying pipe material transfer system, and ensuring quality
- Summary
- Abstract
- Description
- Claims
- Application Information
AI Technical Summary
Problems solved by technology
Method used
Image
Examples
Embodiment 1
[0041] see Figure 3 to Figure 17 The double-head spinning system 1 of the present invention includes a control unit and a feeding device 11 controlled by the control unit, a positioning device 17, a double-head spinning device 12, a double-head cutting device 15, a double-head chamfering device 16, Unloading device 18 and tube material transfer system 13; Tube material transfer system 13 is used for loading such as figure 2 The pipe sections 010 shown are sequentially transferred to corresponding processing stations for processing by corresponding devices. In this embodiment, the feeding device 11, the pipe end positioning device 17, the double-head spinning device 12, the double-head cutting device 15, the double-head chamfering device 16, the unloading device 18 and the pipe material transfer system 13 are all installed On the rack 10, the rack 10 can be constructed by using multiple independent sub-racks, or can be constructed by using an integrated rack. In this embodim...
Embodiment 2
[0062] As the description of Embodiment 2 of the double-head spinning system of the present invention, only the differences from Embodiment 1 of the above-mentioned double-head spinning system will be described below.
[0063] see Figure 18 , in this double-head spinning system 1, the feeding device 11 is constructed with a long tube feeding device 71, and it only uses a chipless rotary cutting head 72 to cut the long tube material, so that the diameter of the tube can be adjusted Larger tubes are loaded.
[0064] Embodiment of double-head spinning method
[0065] In this embodiment, taking the tube material spinning process of the above-mentioned double-head spinning system as an example, the double-head spinning method of the present invention is exemplarily described, and all the contents in the above-mentioned double-head spinning system embodiment are imported into In this embodiment, this embodiment is processed. Specifically, the double-head spinning method of the p...
Embodiment 3
[0076] The embodiment of the double-head spinning system of the present invention includes a processor and a memory, and the memory stores a computer program. When the computer program is executed by the processor, the steps of the above-mentioned double-head spinning method embodiment can be implemented.
[0077] In the above-mentioned embodiment, "pipe end trimming treatment" includes but not limited to pipe end cutting and flattening treatment, and / or pipe end chamfering treatment, and / or pipe end turning inner hole treatment; for the second pipe material processing, also Pipe end processing devices other than pipe end trimming can be used for processing, for example, hole pulling processing, notching processing, pipe bending processing, etc., and are not limited to the pipe end trimming processing in this embodiment. "Used to spin the two ends of the pipe material statically clamped on the pipe material spinning die" and "used to process the two ends of the pipe material st...
PUM
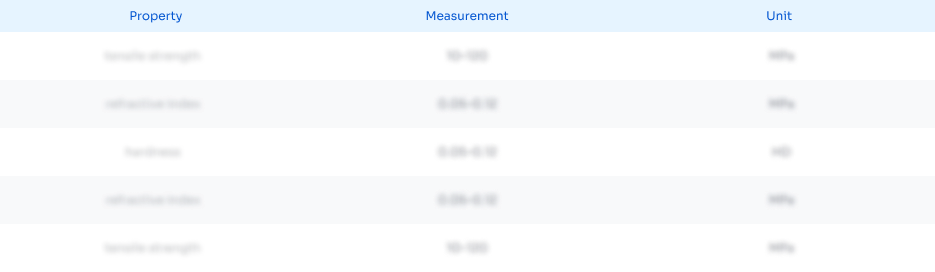
Abstract
Description
Claims
Application Information

- R&D
- Intellectual Property
- Life Sciences
- Materials
- Tech Scout
- Unparalleled Data Quality
- Higher Quality Content
- 60% Fewer Hallucinations
Browse by: Latest US Patents, China's latest patents, Technical Efficacy Thesaurus, Application Domain, Technology Topic, Popular Technical Reports.
© 2025 PatSnap. All rights reserved.Legal|Privacy policy|Modern Slavery Act Transparency Statement|Sitemap|About US| Contact US: help@patsnap.com