Epoxy resin anticorrosive coating with fluoropolymer modified montmorillonite as well as preparation method and application of coating
An epoxy resin and anti-corrosion coating technology, applied in the field of material science, can solve the problems of loss of hydrophobicity, reduced hydrophilicity, limited hydrophobicity, etc. The effect of long-lasting hydrophobicity
- Summary
- Abstract
- Description
- Claims
- Application Information
AI Technical Summary
Problems solved by technology
Method used
Image
Examples
Embodiment 1
[0059] (1) Preparation of fluorine-containing poly(meth)acrylate emulsion
[0060] Weigh 12 g of methacryloxyethyltrimethylammonium chloride, 12 g of glycidyl methacrylate, 30 g of dodecafluoroheptyl methacrylate, and 6 g of methyl methacrylate. The four monomers were mixed and added to 330 g of deionized water, and then mechanically stirred at 700 rpm to form a uniform dispersion. The temperature of the dispersion liquid system was raised to 80°C, 2.4g of potassium persulfate was added, and the reaction was maintained at a constant temperature and stirring speed for 6 hours to obtain a fluorine-containing silicon polymethacrylate emulsion. After the system was cooled, the solid content of the fluorine-containing silicon polymethacrylate emulsion was determined to be about 19.5%.
[0061] (2) Preparation of fluorine-containing poly(meth)acrylate modified montmorillonite
[0062] Disperse 5 g of PGN-type sodium montmorillonite in 500 ml of deionized water, heat to 80° C., and...
Embodiment 2
[0071] (1) Preparation of fluorine-containing poly(meth)acrylate emulsion
[0072] Weigh 20 g of methacryloxyethyl dimethyl benzyl ammonium chloride, 15 g of glycidyl methacrylate, 50 g of hexafluorobutyl methacrylate, and 5 g of dodecyl methacrylate. The four monomers were mixed and added to 800 g of deionized water, and mechanically stirred at 750 rpm to form a uniform dispersion. The temperature of the dispersion liquid system was raised to 85°C, 4g of potassium persulfate was added, and the reaction was maintained at a constant temperature and stirring speed for 5 hours to obtain a fluorine-containing silicon polymethacrylate emulsion. After the system was cooled, the solid content of the fluorine-containing silicon polymethacrylate emulsion was determined to be about 9.8%.
[0073] (2) Preparation of fluorine-containing poly(meth)acrylate modified montmorillonite
[0074] Disperse 10g of PGV-type sodium montmorillonite in 600ml of deionized water, heat to 90°C, and stir...
Embodiment 3
[0083] (1) Preparation of fluorine-containing poly(meth)acrylate emulsion
[0084] Weigh 14 g of acryloyloxyethyl dimethylglycidyl ammonium chloride, 15 g of glycidyl acrylate, 20 g of trifluorooctyl acrylate, and 5 g of hydroxypropyl acrylate. The four monomers were mixed and added to 380 g of deionized water, and mechanically stirred at 900 rpm to form a uniform dispersion. The temperature of the dispersion liquid system was raised to 90°C, 2.7g of potassium persulfate was added, and the reaction was maintained at a constant temperature and stirring speed for 5.5 hours to obtain a fluorine-containing silicon polymethacrylate emulsion. After the system was cooled, the solid content of the fluorine-containing silicon polymethacrylate emulsion was determined to be about 14.5%.
[0085] (2) Preparation of fluorine-containing poly(meth)acrylate modified montmorillonite
[0086] Disperse 8g of PGW-type sodium montmorillonite in 500ml of deionized water, heat to 85°C, and stir at...
PUM
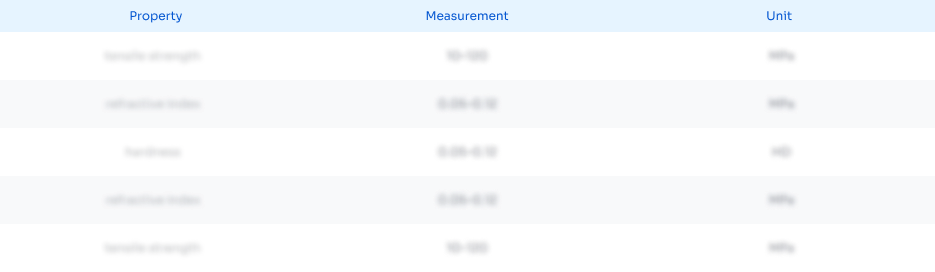
Abstract
Description
Claims
Application Information

- R&D Engineer
- R&D Manager
- IP Professional
- Industry Leading Data Capabilities
- Powerful AI technology
- Patent DNA Extraction
Browse by: Latest US Patents, China's latest patents, Technical Efficacy Thesaurus, Application Domain, Technology Topic, Popular Technical Reports.
© 2024 PatSnap. All rights reserved.Legal|Privacy policy|Modern Slavery Act Transparency Statement|Sitemap|About US| Contact US: help@patsnap.com