Amphoteric monomer and amphoteric polycarboxylic acid water reducer
A technology of amphoteric monomers and water reducers, which is applied in the preparation of sulfonate, chemical instruments and methods, and the preparation of amino hydroxyl compounds. It can solve the corrosion of reinforced concrete and other problems, and achieve the elimination of rust. The synthesis process is simple and the reaction conditions are mild. Effect
- Summary
- Abstract
- Description
- Claims
- Application Information
AI Technical Summary
Problems solved by technology
Method used
Image
Examples
Embodiment 1
[0041] A preparation method of an amphoteric monomer, comprising the steps of:
[0042] (1) Preparation of 6-dimethylaminohexyl methacrylate intermediate
[0043] Add 21.9732g of 6-dimethylamino-1-hexanol and 100mL of ether into a three-neck round bottom flask; control the reaction temperature at 0°C; add 12.3403g of methacryloyl chloride dropwise into the reaction flask for 40min, and then After reacting for 3 hours, stop the reaction; wash the oil layer with deionized water for 3 times, then add a desiccant anhydrous calcium chloride to dry overnight, and the filtrate is rotary evaporated at 35°C to remove the organic solvent ether; to obtain methacrylic acid-6-di The methylaminohexyl ester intermediate is standby;
[0044] (2) Preparation of Amphoteric Monomer
[0045] Add 2.7670g of 6-dimethylaminohexyl methacrylate intermediate, 0.0390g of hydroquinone and 30mL of acetone into a three-neck round bottom flask, stir and dissolve; rise to the reaction temperature of 50°C; ...
Embodiment 2
[0047] A preparation method of an amphoteric monomer, comprising the steps of:
[0048] (1) Preparation of 6-dimethylaminohexyl methacrylate intermediate
[0049] Add 11.0719g of 6-dimethylamino-1-hexanol and 70mL of diethyl ether into a three-neck round bottom flask; control the reaction temperature at 5°C; add 6.2734g of methacryloyl chloride dropwise into the reaction flask for 60min, and then After reacting for 4 hours, stop the reaction; wash the oil layer with deionized water for 3 times, then add a desiccant anhydrous calcium chloride to dry overnight, and the filtrate is rotary evaporated at 35°C to remove the organic solvent ether; to obtain methacrylic acid-6-di The methylaminohexyl ester intermediate is standby;
[0050] (2) Preparation of Amphoteric Monomer
[0051]Add 5.4956g of 6-dimethylaminohexyl methacrylate intermediate, 0.0652g of hydroquinone and 50mL of acetone into a three-neck round bottom flask, stir and dissolve; rise to a reaction temperature of 50°...
Embodiment 3
[0053] A preparation method of an amphoteric monomer, comprising the steps of:
[0054] (1) Preparation of 6-dimethylaminohexyl methacrylate intermediate
[0055] Add 7.2653g of 6-dimethylamino-1-hexanol and 50mL of ether into a three-neck round bottom flask; control the reaction temperature at 5°C; add 5.225g of methacryloyl chloride dropwise into the reaction flask for 60min, and then After reacting for 4 hours, stop the reaction; wash the oil layer with deionized water for 3 times, then add a desiccant anhydrous calcium chloride to dry overnight, and the filtrate is rotary evaporated at 35°C to remove the organic solvent ether; to obtain methacrylic acid-6-di The methylaminohexyl ester intermediate is standby;
[0056] (2) Preparation of Amphoteric Monomer
[0057] Add 6.4950g of 6-dimethylaminohexyl methacrylate intermediate, 0.0732g of hydroquinone and 50mL of acetone into a three-neck round-bottomed flask, stir and dissolve; rise to the reaction temperature of 50°C; di...
PUM
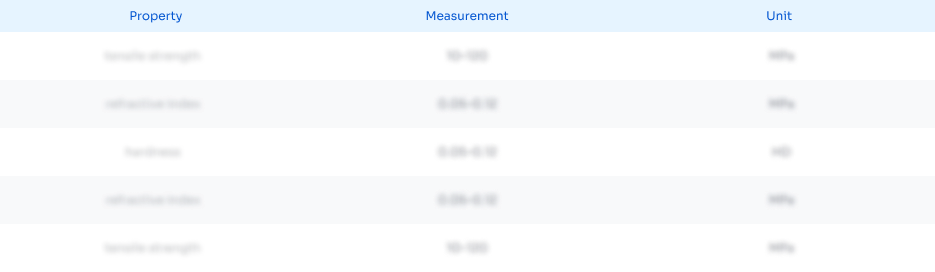
Abstract
Description
Claims
Application Information

- R&D
- Intellectual Property
- Life Sciences
- Materials
- Tech Scout
- Unparalleled Data Quality
- Higher Quality Content
- 60% Fewer Hallucinations
Browse by: Latest US Patents, China's latest patents, Technical Efficacy Thesaurus, Application Domain, Technology Topic, Popular Technical Reports.
© 2025 PatSnap. All rights reserved.Legal|Privacy policy|Modern Slavery Act Transparency Statement|Sitemap|About US| Contact US: help@patsnap.com