Anti-cavitation erosion polyurethane elastic layer and preparation method thereof
A polyurethane elasticity and cavitation technology, applied in the field of elastic layers, can solve the problems of material performance decline, corrosion resistance, shortened service life, etc., and achieve the effects of good tensile performance, good environmental resistance, and adjustable hardness
- Summary
- Abstract
- Description
- Claims
- Application Information
AI Technical Summary
Problems solved by technology
Method used
Image
Examples
preparation example Construction
[0024] The preparation method of the anti-cavitation polyurethane elastic layer of the present invention, wherein
[0025] Step 1: Under the condition of dry inert gas protection, add isocyanate and polyether polyol into an anhydrous airtight container with stirring device, heat and stir under vacuum for a period of time to make it evenly mixed, then further increase the temperature to make the mixture fully React to obtain the prepolymer, that is, component A, and pour it into a dry airtight storage tank for storage
[0026] Step 2: Pour components A and B into a beaker, stir evenly, perform defoaming treatment, and then pour into corresponding molds.
[0027] Step 3: After curing at 80° C. for a period of time, continue curing at room temperature for more than 7 days, so as to obtain a polyurethane coating.
Embodiment 1
[0029] The polyisocyanate in component A is MDI-100, which should be heated to 60°C before use to liquefy it. Weigh 106g and pour it into a 500ml three-necked flask; the polyether polyol should be PPG-1000, which needs to be vacuum removed at 120°C before use. Water 3h, the weighed quality is 173g. Pour it into a three-necked flask and mix it with MDI. Under a nitrogen atmosphere, mechanically stir at 50°C for 1h (380r / min), then raise the temperature to 80°C for 2h rapid reaction to obtain a prepolymer, which is sealed and dried.
[0030] The cross-linking agent of component B is 1,4 butanediol, the cross-linking agent is 330N, and the defoaming agent is 530N. Weigh 120g of prepolymer, 8.9g of 1,4 butanediol, 21g of 330N polyether, and 1.5g of 530N defoamer. Add to a 250ml beaker in sequence, stir mechanically for 2 minutes, vacuumize and defoam in a vacuum box for 25 minutes, pour it into a mold, continue defoaming for 20 minutes, then cure on a heating plate at 80°C for 1...
Embodiment 2
[0032] The polyisocyanate of component A is MDI-50, which should be heated to 50°C to enhance its fluidity before use. Weigh 50g and pour it into a 500ml three-necked flask; Water for 3 hours, the weighed mass is 200g. Pour it into a three-necked flask and mix it with MDI. Under a nitrogen atmosphere, stir mechanically at 50°C for 1h (340r / min), then raise the temperature to 80°C for 2h to obtain a prepolymer, which is sealed and dried.
[0033] The cross-linking agent of component B is 1,4 butanediol, the cross-linking agent is TEA, and the defoaming agent is 530N. Weigh 120g of prepolymer, 2.06g of 1,4 butanediol, 2.27g of TEA, and 1.20g of 530N defoamer. Add to a 250ml beaker one by one, mechanically stir for 2 minutes, vacuumize and defoam in a vacuum box for 10 minutes, pour into a mold, continue defoaming for 15 minutes, cure on a heating plate at 80°C for 12 hours, and finally place it at room temperature for 7 days to complete curing .
PUM
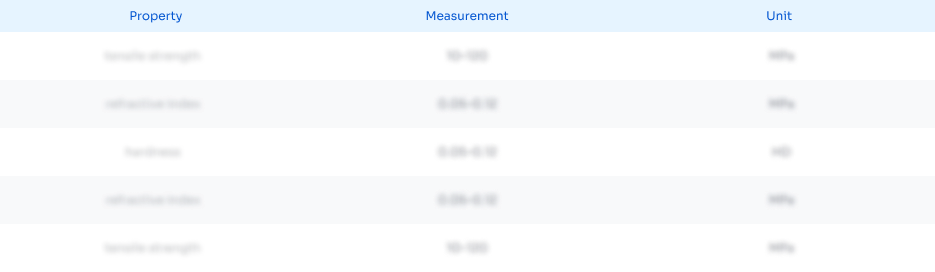
Abstract
Description
Claims
Application Information

- R&D
- Intellectual Property
- Life Sciences
- Materials
- Tech Scout
- Unparalleled Data Quality
- Higher Quality Content
- 60% Fewer Hallucinations
Browse by: Latest US Patents, China's latest patents, Technical Efficacy Thesaurus, Application Domain, Technology Topic, Popular Technical Reports.
© 2025 PatSnap. All rights reserved.Legal|Privacy policy|Modern Slavery Act Transparency Statement|Sitemap|About US| Contact US: help@patsnap.com