Method for improving heat conduction performance of mixed explosive
A technology of thermal conductivity and mixed explosives, which is applied in the direction of non-explosive/non-thermal agent components, explosives, non-explosive fillers/gelling agents/thickeners, etc., which can solve the problem that the efficiency of thermal conductivity is not high enough, the preparation method has not been reported, Problems such as the large amount of thermally conductive fillers are used to achieve the effects of easy scale-up and preparation, significant lifting effect, and improved thermal conductivity
- Summary
- Abstract
- Description
- Claims
- Application Information
AI Technical Summary
Problems solved by technology
Method used
Image
Examples
Embodiment 1
[0028] figure 1 It is a process flow chart of a method for improving the thermal conductivity of mixed explosives of the present invention.
[0029] Weigh 0.5g of Huimo ink ingot, grind it with water in the inkstone, add 0.03g of polyvinyl alcohol and water, and then disperse it for 5min with ultrasound at a frequency of 20kHz to prepare 25g of ink suspension. Weigh 47.5g of 1,3,5-triamino-2,4,6-trinitrobenzene explosive, add 50g of water, and add 12.5g of prepared ink suspension, stir and disperse to form composite explosive suspension. Heat up to 60°C, add half of the binder solution containing 2g of fluororubber dropwise, and apply vacuum to remove the organic solvent. Then add the remaining 12.5g of ink suspension, and add dropwise the remaining half of the binder solution containing 2g of fluororubber, and continue to apply vacuum treatment to prepare explosive modeling powder, which is filtered, washed with water, dried, and pressed into medicine column, the mixed expl...
Embodiment 2
[0031] Weigh 4g of Huimo ink stick, grind it with water in the inkstone, add 0.4g of alkylphenol polyoxyethylene ether and water, and then disperse it for 15min with ultrasound at a frequency of 60kHz to prepare 80g of ink suspension. Weigh 190g of hexanitrohexaazaisopentazane explosive, add 200g of water, and add 50g of prepared ink suspension, stir and disperse to form composite explosive suspension. Heat to 60° C., add half of the binder solution containing 6 g of polyurethane dropwise, and apply vacuum to remove the organic solvent. Then add the remaining 30g of ink suspension, and drop the remaining half of the binder solution containing 6g of polyurethane, and continue to apply vacuum treatment to prepare explosive modeling powder, which is filtered, washed with water, dried, and pressed into a powder column. The mixed explosive with significantly improved thermal conductivity can be obtained. The thermal conductivity test was carried out by the laser flash method, and ...
Embodiment 3
[0033] Weigh 2.4g of Huimo ink stick, grind it with water in the inkstone, add 2.4 polyvinylpyrrolidone and water, and then disperse for 30min with ultrasound at a frequency of 80kHz to prepare 240g of ink suspension. Weigh 190g of Oktokin explosive, add 200g of water, and add 120g of prepared ink suspension, stir and disperse to form composite explosive suspension. The temperature was raised to 60° C., half of the binder solution containing 7.6 g of vinyl acetate cellulose was added dropwise, and vacuum was applied to remove the organic solvent. Then add the remaining 120g ink suspension, and drop the remaining half of the binder solution containing 7.6g vinyl acetate cellulose, continue to apply vacuum treatment, prepare explosive molding powder, filter, wash with water, dry, and By pressing it into a charge column, a mixed explosive with significantly improved thermal conductivity can be obtained. The thermal conductivity test was carried out by the laser flash method, and...
PUM
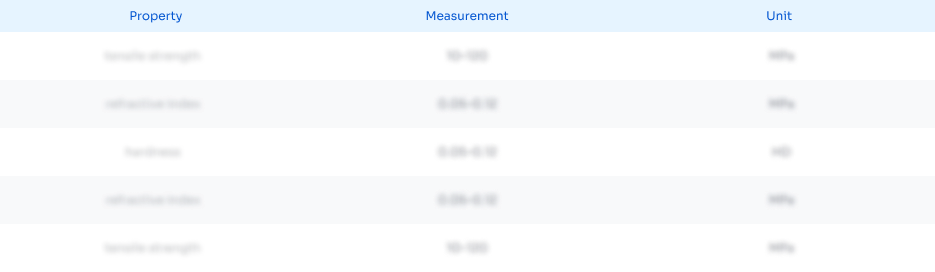
Abstract
Description
Claims
Application Information

- R&D Engineer
- R&D Manager
- IP Professional
- Industry Leading Data Capabilities
- Powerful AI technology
- Patent DNA Extraction
Browse by: Latest US Patents, China's latest patents, Technical Efficacy Thesaurus, Application Domain, Technology Topic, Popular Technical Reports.
© 2024 PatSnap. All rights reserved.Legal|Privacy policy|Modern Slavery Act Transparency Statement|Sitemap|About US| Contact US: help@patsnap.com