Mineral separation method for recovering cassiterite from tin-copper paragenic ore
A mineral processing method and symbiotic ore technology, applied in the field of mineral processing, can solve problems such as difficulty in ensuring simple recovery process, affecting cassiterite flotation operations, and increasing the cost of flotation reagents, so as to optimize the cassiterite flotation environment and reduce ore slime Effects of loss and increase in optionality
- Summary
- Abstract
- Description
- Claims
- Application Information
AI Technical Summary
Problems solved by technology
Method used
Image
Examples
Embodiment 1
[0034] Schematic diagram of cassiterite recovery process figure 1 As shown, the specific process is:
[0035] S1. Grinding the raw ore to -0.074mm accounts for 75%; adjust the pulp concentration to 30%;
[0036] S2. Flotation of copper sulfur: 80 g / ton of copper chloride, 100 g / ton of methyl isobutyl carbinol xanthate, 30 g / ton of terpineol oil and ethylthiourethane mixed in a mass ratio of 1:1 are added in sequence. Ton for a rough selection; add methyl isobutyl carbinol xanthate 35 g / ton, terpineol oil and thiocarbamate mixed at a mass ratio of 10 g / ton to do a sweep; add methyl isobutyl 20 g / ton of butyl carbinol xanthate, 10 g / ton of terpineol oil and thiocarbamate mixed at a mass ratio of 1:1 are used for secondary sweeping; the rough selection foam is used for secondary blank selection; copper-sulfur Mixed concentrate and floating sulfur tailings;
[0037] S3. Magnetic separation: use a high-gradient strong magnetic separator for floating sulfur tailings to perform ma...
Embodiment 2
[0041] The raw ore sample that this example uses is with example 1. The specific cassiterite recovery process is the same as in Example 1, except that the floating sulfur tailings in step S3 are subjected to strong magnetic separation under the condition of a background field strength of 0.4T to obtain magnetic separation concentrate and magnetic separation tailings; in step S4 As shown in Table 1 of the medicament and its consumption part that adopts, obtain tin grade and be 6.32%, tin recovery rate is 86.15% float tin concentrate and float tin tailings; Then according to the S5 step among the embodiment 1, float tin concentrate The Nelson centrifugal concentrator was used for separation to obtain a tin concentrate with a tin grade of 40.25% and a recovery rate of 75.77% and a tin sub-concentrate with a tin grade of 0.88% and a recovery rate of 10.38%.
Embodiment 3
[0043] The raw ore sample that this example uses is with example 1. The specific cassiterite recovery process is the same as in Example 1, except that the floating sulfur tailings in step S3 are subjected to strong magnetic separation under the condition of a background field strength of 0.4T to obtain magnetic separation concentrate and magnetic separation tailings; in step S4 As shown in the medicament and consumption part table 1 of adopting, obtain tin grade and be 6.56%, tin recovery rate is 86.62% floating tin concentrate and floating tin tailings; Then according to the S5 step among the embodiment 1, the floating tin concentrate The Nelson centrifugal concentrator was used for separation to obtain tin concentrate with a tin grade of 40.13% and a recovery rate of 75.77% and a tin sub-concentrate with a tin grade of 0.96% and a recovery rate of 10.85%.
PUM
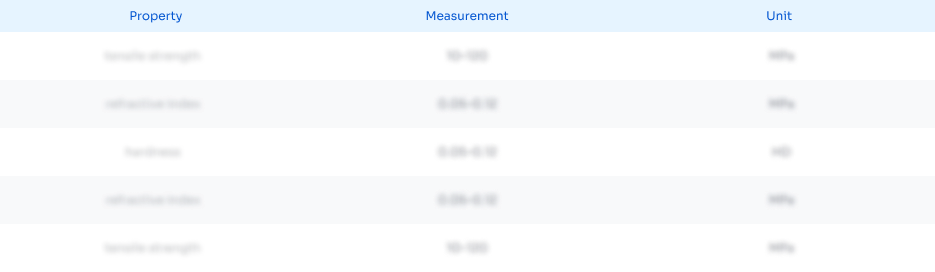
Abstract
Description
Claims
Application Information

- Generate Ideas
- Intellectual Property
- Life Sciences
- Materials
- Tech Scout
- Unparalleled Data Quality
- Higher Quality Content
- 60% Fewer Hallucinations
Browse by: Latest US Patents, China's latest patents, Technical Efficacy Thesaurus, Application Domain, Technology Topic, Popular Technical Reports.
© 2025 PatSnap. All rights reserved.Legal|Privacy policy|Modern Slavery Act Transparency Statement|Sitemap|About US| Contact US: help@patsnap.com