Stress, temperature and vibration composite detection optical fiber sensor and signal processing method
A fiber optic sensor and composite detection technology, applied in the direction of converting sensor output, using optical devices to transmit sensing components, instruments, etc., can solve problems such as system errors, optical fiber physical quantities are not completely the same, and dynamic vibration signals cannot be detected, so as to reduce errors. High reporting rate, low noise level and high positioning accuracy
- Summary
- Abstract
- Description
- Claims
- Application Information
AI Technical Summary
Problems solved by technology
Method used
Image
Examples
Embodiment Construction
[0041] In order to make the object, technical solution and advantages of the present invention clearer, the present invention will be further described in detail below in conjunction with the accompanying drawings.
[0042] Such as figure 1, a stress, temperature and vibration composite detection optical fiber sensor according to an embodiment of the present invention, comprising a laser light source 1, a first 1:1 coupler 2, a 1:99 coupler 3, an acousto-optic modulator 4, and an erbium-doped fiber amplifier 5 , the first circulator 6, the sensing fiber 7, the second circulator 8, the second 1:1 coupler 9, the first photodetector 10, the down conversion filter circuit 11, the data acquisition system and the upper computer 12, the first Electro-optic modulator 13, first microwave generator 14, fiber isolator 15, auxiliary fiber 16, third 1:1 coupler 17, reference fiber 18, second electro-optic modulator 19, second microwave generator 20, filter grating 21. A fourth 1:1 coupler...
PUM
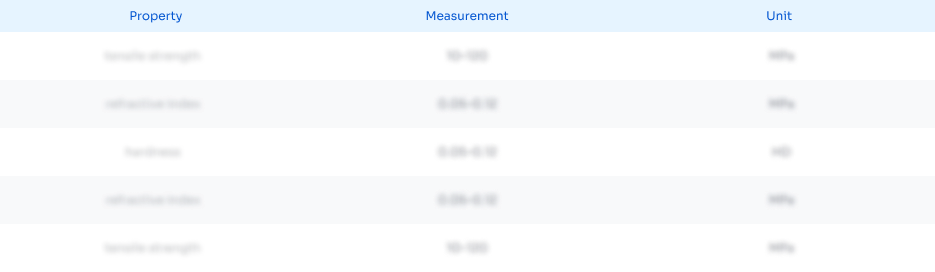
Abstract
Description
Claims
Application Information

- R&D Engineer
- R&D Manager
- IP Professional
- Industry Leading Data Capabilities
- Powerful AI technology
- Patent DNA Extraction
Browse by: Latest US Patents, China's latest patents, Technical Efficacy Thesaurus, Application Domain, Technology Topic, Popular Technical Reports.
© 2024 PatSnap. All rights reserved.Legal|Privacy policy|Modern Slavery Act Transparency Statement|Sitemap|About US| Contact US: help@patsnap.com