Metal mesh and mesh rack plastic-dipping heating furnace
A metal mesh and heating furnace technology, which is applied in the direction of pretreatment surface, coating, device for coating liquid on the surface, etc. and other problems, to achieve the effect of rapid and uniform heat distribution, better heating effect, and convenient heating work.
- Summary
- Abstract
- Description
- Claims
- Application Information
AI Technical Summary
Problems solved by technology
Method used
Image
Examples
Embodiment 1
[0031] refer to Figure 1-3 , a kind of metal mesh grid frame dipping heating furnace, comprising a furnace body 1, a plurality of support legs 2 are fixedly connected to the lower side wall of the furnace body 1, and a roller 3 is arranged at the lower end of each support leg 2, and the roller 3 To move the furnace body 1, a feed inlet 11 is provided on one side wall of the furnace body 1, and a placement device and a plurality of heating wires 15 are arranged between the inner walls of both sides of the furnace body 1. 1 A plurality of rollers 12 between the inner walls on both sides, the plurality of rollers 12 are located above the heating wire 15, the heating wire 15 heats the air in the furnace body 1, and the heated air passes through the gap between the rollers 12 upwards It contacts with the metal mesh to realize the uniform distribution of the airflow and complete the heating of the metal mesh. The inner wall of the feed port 11 is connected with the door plate 16 th...
Embodiment 2
[0035] refer to Figure 4 , a kind of metal mesh frame dipping heating furnace, comprising a furnace body 1, the lower side wall of the furnace body 1 is fixedly connected with a plurality of support legs 2, the lower end of each support leg 2 is provided with a roller 3, through the roller 3 To move the furnace body 1, a feed port 11 is provided on one side wall of the furnace body 1, a placement device and a plurality of heating wires 15 are arranged between the inner walls of both sides of the furnace body 1, and the placement device is fixed on the furnace body 1 The intubation tubes on the inner walls of both sides are vertically inserted with an insertion rod, and the outer wall of the insertion rod is fixed with a horizontally arranged supporting plate 17, and two U-shaped rods 18 are inserted on the outer side of the furnace body 1, two U-shaped bar 18 is positioned at one end in body of heater 1 and is fixed with splint 19, and the upper side wall of body of heater 1 ...
PUM
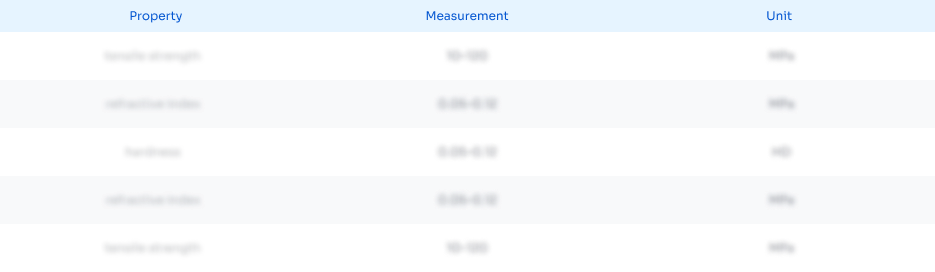
Abstract
Description
Claims
Application Information

- R&D
- Intellectual Property
- Life Sciences
- Materials
- Tech Scout
- Unparalleled Data Quality
- Higher Quality Content
- 60% Fewer Hallucinations
Browse by: Latest US Patents, China's latest patents, Technical Efficacy Thesaurus, Application Domain, Technology Topic, Popular Technical Reports.
© 2025 PatSnap. All rights reserved.Legal|Privacy policy|Modern Slavery Act Transparency Statement|Sitemap|About US| Contact US: help@patsnap.com