System and method for resource recycling of vanadium-titanium-tungsten series denitration catalysts and water recycling use
A catalyst and resource-based technology, applied in chemical instruments and methods, chemical recycling, water/sewage treatment, etc., can solve problems such as water recycling and secondary pollution that have not been paid attention to, to improve purity, reduce waste water generation, The effect of simple process operation
- Summary
- Abstract
- Description
- Claims
- Application Information
AI Technical Summary
Problems solved by technology
Method used
Image
Examples
Embodiment 1
[0050] The waste vanadium-titanium-tungsten denitrification catalyst is cleaned, crushed, ground and sieved in the pretreatment unit 1 to make a powder with a particle size of less than 100 mesh, which is sent to the reaction chamber of the alkali leaching unit 2 using sodium hydroxide; It is a 40% NaOH solution, in which the solid-to-liquid ratio of the catalyst powder to the NaOH solution is 1g:5mL, then heated to 80°C, and stirred at a constant temperature for 4 hours; the reaction product is filtered to obtain a TiO-containing 2 The precipitate and the basic filtrate containing vanadium and tungsten; the filtrate is sent to the reaction chamber of the pH adjustment unit 3 using sulfuric acid, and the mass fraction of 30% H is added 2 SO 4 The solution is adjusted to a pH value of 11, filtered after standing for 12 hours, and the crystals are removed. After the filtrate is adjusted to pH=11, it is transported to the reaction chamber of the ammonium sulfate vanadium precipit...
Embodiment 2
[0052] The waste vanadium-titanium-tungsten denitrification catalyst is cleaned, crushed, ground and sieved in the pretreatment unit 1 to make a powder with a particle size of no more than 100 mesh, which is sent to the reaction chamber of the alkali leaching unit 2 using sodium hydroxide; NaOH solution with a fraction of 30%, wherein the solid-to-liquid ratio of the catalyst powder to the NaOH solution is 1g:4mL, then heated to 100°C, and stirred at a constant temperature for 6 hours; the reaction product is filtered to obtain a TiO-containing 2 The precipitate and the basic filtrate containing vanadium and tungsten; the filtrate is sent to the reaction chamber of the pH adjustment unit 3 using sulfuric acid, and the mass fraction of 40% H is added 2 SO 4 The solution is adjusted to a pH value of 8, filtered after standing for 12 hours, and the crystals are removed. After the filtrate is adjusted to pH=12, it is transported to the reaction chamber of the ammonium sulfate vana...
Embodiment 3
[0054] The waste vanadium-titanium-tungsten denitrification catalyst is cleaned, crushed, ground and sieved in the pretreatment unit 1 to make a powder with a particle size of no more than 100 mesh, which is sent to the reaction chamber of the alkali leaching unit 2 using sodium hydroxide; NaOH solution with a fraction of 50%, wherein the solid-to-liquid ratio of the catalyst powder to the NaOH solution is 1g:10mL, then heated to 90°C, and stirred at a constant temperature for 2 hours; the reaction product is filtered to obtain a TiO-containing 2 The precipitate and the basic filtrate containing vanadium and tungsten; the filtrate is sent to the reaction chamber of the pH adjustment unit 3 using sulfuric acid, and the mass fraction of 50% H is added 2 SO 4 The solution is adjusted to a pH value of 12, filtered after standing for 12 hours, and the crystals are removed. After the filtrate is adjusted to pH=11, it is transported to the reaction chamber of the ammonium sulfate van...
PUM
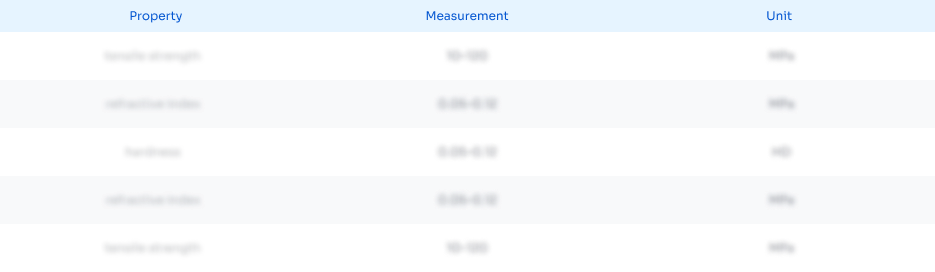
Abstract
Description
Claims
Application Information

- R&D Engineer
- R&D Manager
- IP Professional
- Industry Leading Data Capabilities
- Powerful AI technology
- Patent DNA Extraction
Browse by: Latest US Patents, China's latest patents, Technical Efficacy Thesaurus, Application Domain, Technology Topic, Popular Technical Reports.
© 2024 PatSnap. All rights reserved.Legal|Privacy policy|Modern Slavery Act Transparency Statement|Sitemap|About US| Contact US: help@patsnap.com