Offset Steering Mechanism and Control Method of Static Pointing Rotary Steerable Drilling Tool
A technology of rotary steerable drilling and steering mechanism, which is used in directional drilling, driving devices for drilling in wellbore, drilling equipment, etc., can solve the problems of high drilling fluid sealing requirements, deformation, and difficulty in increasing precise hydraulic steering control.
- Summary
- Abstract
- Description
- Claims
- Application Information
AI Technical Summary
Problems solved by technology
Method used
Image
Examples
Embodiment Construction
[0045] The preferred embodiments of the present invention will be described in detail below in conjunction with the accompanying drawings; it should be understood that the preferred embodiments are only for illustrating the present invention, rather than limiting the protection scope of the present invention.
[0046] Such as Figure 1 to Figure 3 As shown, the offset guide mechanism of the static pointing rotary steerable drilling tool includes a non-rotating outer cylinder 10, a drill bit 11, a drill bit connecting shaft 1, a flexible hose 5, a slider connector 9, a guide mechanism housing 17 and a bias mechanism , The biasing mechanism is provided with two groups, and is installed in the non-rotating outer cylinder 10 perpendicular to each other, and the adjustment directions of the two biasing mechanisms are the X direction and the Y direction.
[0047] Specifically, the drill bit connecting shaft 1 is a hollow body, and the hollow part is used as a circulation channel for...
PUM
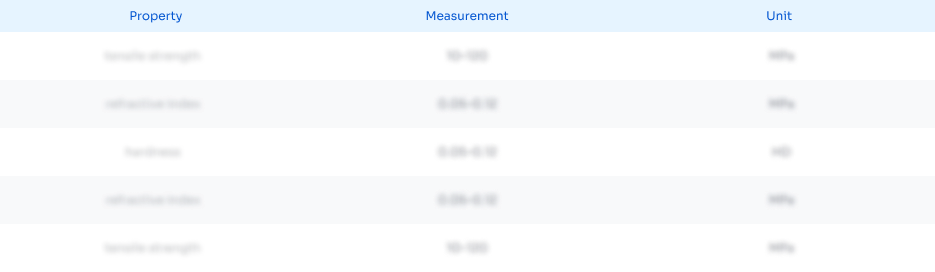
Abstract
Description
Claims
Application Information

- R&D
- Intellectual Property
- Life Sciences
- Materials
- Tech Scout
- Unparalleled Data Quality
- Higher Quality Content
- 60% Fewer Hallucinations
Browse by: Latest US Patents, China's latest patents, Technical Efficacy Thesaurus, Application Domain, Technology Topic, Popular Technical Reports.
© 2025 PatSnap. All rights reserved.Legal|Privacy policy|Modern Slavery Act Transparency Statement|Sitemap|About US| Contact US: help@patsnap.com