Efficient dyeing process for improving anti-felting performance of wool fabric
A technology for anti-felt shrinkage and fabrics, applied in the field of garment fabric processing, can solve the problems of increasing dyeable cost, decreasing strength, and hardening of hand feeling, achieving good anti-felt shrinkage, resisting external physical and chemical effects, and accelerating the degree of warping. The effect of increasing and increasing the degree of warping
- Summary
- Abstract
- Description
- Claims
- Application Information
AI Technical Summary
Problems solved by technology
Method used
Image
Examples
Embodiment 1
[0026] A high-efficiency dyeing process for improving the anti-felting performance of wool fabrics, the specific method is as follows:
[0027] 1) Add nano-titanium dioxide to distilled water to prepare a nano-titanium dioxide aqueous solution with a mass percentage of 5%, then add the wool fabric to the nano-titanium dioxide aqueous solution, vibrate for 3 hours under 500W ultrasonic waves, and place the treated wool fabric at 50°C down drying;
[0028]2) Put the dried wool fabric into a vacuum tank with a stirring device, evacuate to 0.02MPa to form a negative pressure, keep it for 2 hours, then add cationic keratin graft polymer powder, at a speed of 1500r / min Stir at high speed under low temperature, then heat to 40°C, apply pressure to the tank to 1MPa through a hydraulic pump, form a positive pressure, keep it for 3 hours, repeat the treatment 3 times according to the above-mentioned negative pressure-positive pressure treatment method;
[0029] 3) Under normal pressure...
Embodiment 2
[0043] A high-efficiency dyeing process for improving the anti-felting performance of wool fabrics, the specific method is as follows:
[0044] 1) Add nano-titanium dioxide to distilled water to prepare a nano-titanium dioxide aqueous solution with a mass percentage of 7%, then add the wool fabric to the nano-titanium dioxide aqueous solution, vibrate for 2.5 hours under 600W ultrasonic waves, and place the treated wool fabric at 55 Dry at ℃;
[0045] 2) Put the dried wool fabric into a vacuum tank with a stirring device, evacuate to 0.03MPa to form a negative pressure, and keep it for 1.5h, then add cationic keratin graft polymer powder, at a speed of 2000r / Stir at a high speed for 1 min, then heat to 45°C, apply pressure to the tank to 1.5 MPa through a hydraulic pump, form a positive pressure, keep it for 2.5 hours, and repeat the treatment 4 times according to the above-mentioned negative pressure-positive pressure treatment method;
[0046] 3) Under normal pressure, put...
Embodiment 3
[0060] A high-efficiency dyeing process for improving the anti-felting performance of wool fabrics, the specific method is as follows:
[0061] 1) Add nano-titanium dioxide to distilled water to prepare a nano-titanium dioxide aqueous solution with a mass percentage of 10%, then add the wool fabric to the nano-titanium dioxide aqueous solution, vibrate for 2 hours under 800W ultrasonic waves, and place the treated wool fabric at 60°C down drying;
[0062] 2) Put the dried wool fabric into a vacuum tank with a stirring device, evacuate to 0.05MPa to form a negative pressure, keep it for 1h, then add cationic keratin graft polymer powder, at a speed of 2500r / min Stir at high speed under low temperature, then heat to 50°C, apply pressure to the tank to 2MPa through a hydraulic pump, form a positive pressure, keep it for 2 hours, repeat the treatment 5 times according to the above-mentioned negative pressure-positive pressure treatment method;
[0063] 3) Under normal pressure, p...
PUM
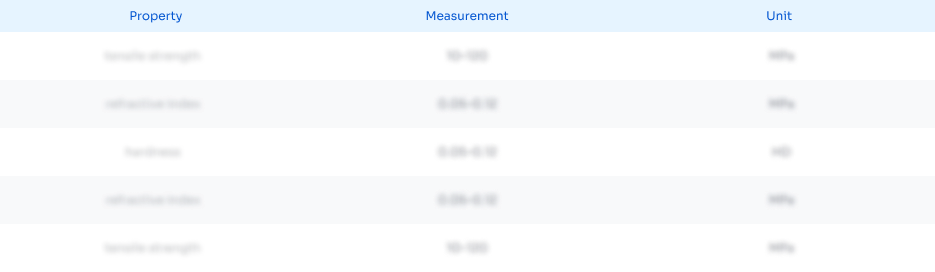
Abstract
Description
Claims
Application Information

- Generate Ideas
- Intellectual Property
- Life Sciences
- Materials
- Tech Scout
- Unparalleled Data Quality
- Higher Quality Content
- 60% Fewer Hallucinations
Browse by: Latest US Patents, China's latest patents, Technical Efficacy Thesaurus, Application Domain, Technology Topic, Popular Technical Reports.
© 2025 PatSnap. All rights reserved.Legal|Privacy policy|Modern Slavery Act Transparency Statement|Sitemap|About US| Contact US: help@patsnap.com